Fukudaco, Japan
Fukudaco MiniCODER Series for Machine Tools
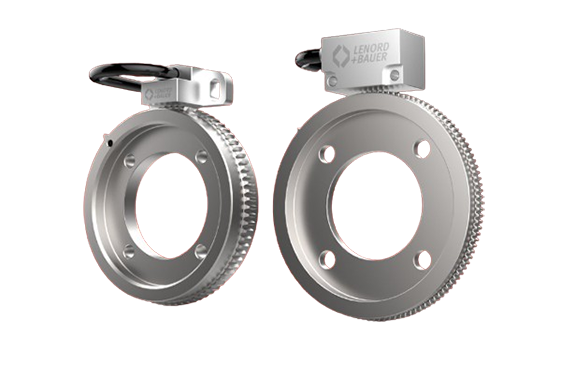
Manufacturer: Fukudaco
Overview
These are non-contact, high-precision, high-speed capable speed and position encoders.
Applications
- Machine tool spindle speed and position detection (ATC)
- High-frequency spindle speed detection
- Radar equipment angle detection
- Speed detection for testing equipment
Features
- Extremely compact sensor head
- Customizable target wheel (detection gear)
- Compatible with Mitsubishi CNC protocols (M800/M80/E80/C80)
- High waterproof and dustproof standards, compliant with IP68
Specification
Sensor head dimensions H x W x D | 15.5(mm) x 37.5(mm) x 21.4(mm) (GEL2444) |
---|---|
Target wheel inner diameter | 8mm and up |
module | 0.3, 0.5, 1.0 |
Output Signal | Sine wave output signal 1Vpp / Square wave output signal TTL / Mitsubishi CNC protocol |
Rotational Speed | Max. 100,000 min -1 possible (depending on target wheel diameter) |
Operating temperature | -30℃~+85℃ |
Protection rating | IP68 |
Target Wheel
The target wheel detected by the sensor head has three structural options for the reference position:
Flag – Slot – Teeth
Each structure has distinct characteristics, allowing you to choose based on your specific needs:
- Flag: Not suitable for high-speed rotation due to structural imbalance, but advantageous in terms of cost.
- Slot: Offers better balance compared to the flag type.
- Teeth: Less cost-effective but provides excellent balance due to being machined, capable of handling speeds up to 100,000 min-1.
Output Signal Waveform
The output signals from the rotary encoder consist of two-phase rotation signals and one-phase reference position signal. The two types of signals output by the rotary encoder are:
- U1, U2: These signals are used for rotation control. You can choose between square wave or sine wave, depending on the specifications of the connected controller.
- UN: This signal is used for positioning control and is output once per revolution. You can choose between a flat (left diagram) or a peaked (right diagram) waveform.
Digital Communication
We provide products compatible with various communication protocols from different manufacturers (some still under development).
On-line Inspection Module GEL211
The on-line inspection module GEL211 allows for the verification and signal correction of the following items in an on-machine state.
- Operating Statistics: Determines the operational duration within various speed ranges.
- Cumulative Operating Time: Tracks the total operating time.
- Signal Waveform: Monitors signal quality.
- Gear Damage Detection: Identifies damage to gears.
- Signal Correction: Performs signal adjustments.
Signal correction and confirmation of accumulated operating time can be done from a PC, tablet, etc. Also, you can set and check from the following browsers you are already using without installing special software.
- Firefox 10+
- Safari 5.0+
- Chrome 16+
- Opera 10+
Related Products
-
TONE 760MS Socket Wrench Set
-
Kanetec HMW Series Waterproof Maghand
-
Vessel No.TA20BSQ3L “GO-TAN” (Hard Forged) Mirror Socket Adapter (3/8″SQ 9.5mm Long)
-
TSUBOSAN QHI-EX11 235mm/150mm ENGINEER’S FILES 150mm SIZE STANDARD BASTARD / SMOOTH EXTREME
-
Kunimoto Big BS Large Front Opening Matek Box M (Dove Plating)
-
NDV FEX100NB type Ball valves with jacket