BINZEL JAPAN Ltd
BINZEL JAPAN MFS-V3 Master Feeder System
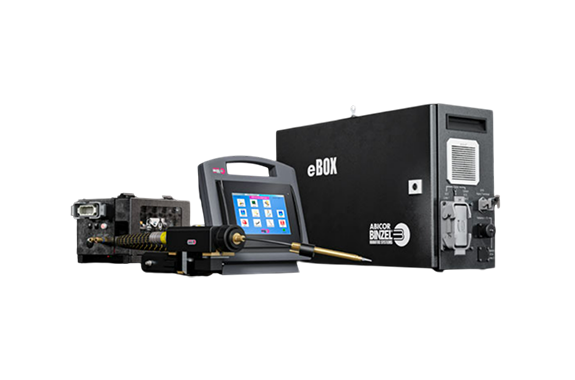
Manufacturer: BINZEL JAPAN.
Product: Master Feeder System
Model: MFS-V3
Overview of the advantages of the MFS-V3 (Master Feeder System)
Performance and functionality:
- Digital wire feeding system with fast and precise control for high-precision laser applications
- Two controlled drives for high-dynamic operations
- Wire buffer function for virtually frictionless wire feeding and low maintenance
- Adjustable tolerance range for the wire speed
- Usable with an in-process drive as a master pull system for short to medium distances
- Wide-range input for different supply voltages globally
- Analogue, digital or field bus activation possible
- Direct operation and job operation mode possible
- Safety circuit in the AIDA version
- Future-oriented, upgradeable structure (modular principle)
- Compatible with MFS-V2 – simple exchange and system upgrade possible
- Option: hot wire available from ABICOR BINZEL
Easy Servicing:
- Extensive service software with visualisation and documentation
- Simple update via SD card slot
- User level release possible using key stick (USB)
- Freely configurable maintenance intervals
- Operating/service software via system PC and/or control panel (MF control)
- Fault memory with a plain text display
- Control panel (MF control) can be used for several systems
Drive optimisation
The proven MF-1 drive was optimized with top vehicle manufacturers to enhance wire feeding performance:
- Complete reworking of the pressure rocker for adjustment to increasing service requirements
- Optimisation of the load transmission to the wire by adjusting the spring tension for different wire thicknesses
- Considerable simplification of the installation resp. dismantling of the wire feed rollers
- A new pressure system at the wire sensor prevents incorrect settings and ensures that the correct wire speed is shown
- Various ceramic wearing parts are available for high requirements to extend the service life and reduce maintenance work
With the MFS-V3, ABICOR BINZEL ROBOTIC SYSTEMS has developed a future-oriented wire feeding system for laser applications that can be integrated optimally into the respective application-specific production environment.
Control sytem eBOX V3 – The nerve centre of the systems
In the third generation of the master feeder system, a comprehensive new development of the eBOX control unit has been used to meet the complex requirements of wire feeding in laser applications. The result is a completely reworked and optimised eBOX with modular and precisely coordinately components. As the nerve centre of the system, it is ideally equipped for the ever-increasing requirement profile in laser applications – particularly in car manufacturing – all over the world.
The eBOX represents the communication interface between the higher-level plant control and the wire drives of the MFS-V3. It houses all the electronic control elements and is available as an analogue/digital version and digitally for various fieldbus systems/interfaces.
Fully digital control circuits as well as consistent separation of logic (Multibus I/O board) and drive technology (axis controller) ensure that individual system components are reproducible in the case of servicing and can be replaced without further adaptation. Time-consuming calibration of analogue tachometer systems or other components therefore belong to the past: fully digital control for a futureproof system.


MFS service software – for complete control
The MFS service software – the comprehensive software package for management, diagnostics, operating status display, fault evaluation and quality recording – was used even in MFS-V2. For the third version of the MFS, the tried and tested service software has been completely reworked, improved and extended with many additional functions.
As usual, the software – which is now licence-free as standard – can be used with the existing system PC in conjunction with an eBOX. As an alternative for managing several eBOX devices, the innovative MF-Control operating panel with fine and precise touchscreen is now also available, making the work of the operator much easier.
The simple and intuitive software user interface allows straightforward use of all functions. For safety, users can be given different usage rights. This is done by assigning a user level. Users can identify themselves and log in with a user login and password or alternatively with a key stick.
The option of job programming in offline mode offers a great advantage that operates independently of the robot, which prevents system standstill. This allows management of several eBOX devices at the same time with software and the MF-Control operating panel.
The main features at a glance:
- Setting and editing of up to 64 different jobs
- Comprehensible documentation of the processes
- Fault display in plain text
- Fault log with analysis and troubleshooting
- Creation and management of freely definable maintenance intervals possible
- Diagnostics: clear system status display, which shows directly whether the system is operational or whether there is a fault
- Several eBOX devices can be given station information by assigning the IP address
- Saved station information is shown in the log files
- Multilingual user interface: six different languages can be selected (German, English, French, Italian, Polish and Spanish)
- Setting the wire buffer function
- Three user levels:
• 0 (read authorisation)
• 1 (authorised to load the config. files)
• 2 (administrator rights)
Flex supply – close to the action
The Flex supply provides optimal feeding of the wire into the process and is ultimately the interface between the wire feeding system and the workpiece. It is fixed to the laser optic and thus adjusts exactly to its movements.
Essentially, the Flex supply comprises the securing nut fitted on the MF1 drive, and the feeding body with wire feeding nozzle. The connection between the two products is made by a flexible liner, which can be shortened as required. Depending on the wire diameter and material, there is also a choice of various liners and wire feeding nozzles.
The feeding body is available both for cold and for hot wire applications. The cold wire variant comes optionally with or without gas feed; the hot wire version is available with gas feeding and cooling. Here, the gas and the coolant are fed separately to the feeding body.
The advantages in brief:
- Can be shortened individually due to the flexible liner between feeding body and securing nut
- Feeding body for cold & hot wire with or without process gas
- Can be adapted to all standard laser optics
- Quick, safe fitting and changing of the body with a specially adjustable clip system
- Excellent accessibility and optimal seam surfaces due to new design with coaxial gas feed
- With the new design, the gas nozzle is no longer required, which reduces the wear parts
Front drive MF1 – the driving force
The robust and powerful MF1 front drive brings the master feeder system to life. Having been developed specifically for laser applications, it scores points with its small size, light weight and variety of connection systems. It can be used individually or in conjunction with the rear drives (master pull or push-push system).
The centrepiece of the MF1 is the 4-roller drive in combination with the fast, digital motor control via the new eBOX. The 4-roller principle guarantees minimum slippage and prevents deformation of the wire as a result of pressure forces. The short acceleration and response times, which are important for laser applications, can therefore be achieved.
The drive/specification speed is monitored and controlled by a built-in encoder. In addition, the actual wire speed is determined with the aid of the actual value transmitter for the wire and forwarded to the service software. The good accessibility and the quality of the wearing parts allow quick and easy replacement of wearing parts and thus reduce downtimes.
The advantages in brief:
- 4-roller drive
- Small size and light weight
- Monitoring of feeding speed by actual value transmitter (AVT) for the wire and service software
- Reworked pressure rocker for adaptation to increasing service requirements
Wire feeding hose MasterLiner – for constant flow
The products in the MasterLiner series set new standards in wire feeding. They consist of individual segments, each of which can be rotated by 360°. Four small rollers in each segment ensure smooth wire feeding with virtually no resistance.
The MasterLiner system is available in the MasterLiner and the MasterLiner MAXI designs, each in the variants HD and FLEX. The flexible FLEX version – consisting of a corrugated tube and variable connection system – allows easy, free assembly of the desired length as well as unproblematic repair directly on site. This advantage saves time and therefore also money.
The heavy duty HD variant is sheathed in a resistant aramid fibre reinforced protective fabric and has been developed for extreme applications.
With the use of the roller-guided MasterLiner, it is no longer necessary to change electrodes – so timeconsuming maintenance work on the cable assembly is avoided. In addition to the improved process stability, further potential for savings is therefore realised and the system availability is significantly increased.
The advantages in brief:
- Low friction forces
- Long durability
- Can be cleaned by ultrasonic bath
- Maintenance free and low susceptibility to faults
- Wire feeding possible over long distances and with only one drive
- Can be used for all types of wire
- Easy, quick setup and replacement due to quick-release
Rear drives – additional power if required
For certain applications, it is recommended to operate the MFS-V3 system with a second drive, as a push-push system, to guarantee reliable processing of the wire feeding.
Wire feeding route length and condition are key factors in decision-making. For long or complex routes, a rear drive ensures smooth feeding. Material properties also matter—soft wires like aluminum need two drives to prevent tensile forces, ensuring even pushing instead of pulling. The extra drive reduces system wear by minimizing component strain. Each drive is independently controlled by the eBOX, eliminating the need for synchronization while maintaining fast response times.
Furthermore, the wire buffer function of the system is new, which is controlled by the intake current of the rear drive. This ensures that the MasterLiner is refilled with enough wire after each cycle. This function guarantees even better wire feeding performance, particularly at the start.
MF1-Rear
Being structurally identical to the MF1 front drive, the MF1-Rear includes also the positive characteristics of the “big brother”. The two are distinguished only by the actual value transmitter for the wire (AVT), which is not required in the MF1-Rear and is therefore omitted.
The identical wear parts system makes it the perfect addition to the main drive.
M-DRIVE
The M-DRIVE has a large and powerful motor, which – like the MF1 master drive and MF1-Rear – is based on the 4-roller principle.
As a rear drive, its special coil carriers make it particularly suitable for wire feeding from the coil.
Operating panel MF-Control – everything in view
The MF-Control operating panel is an optional component of the system and represents the mobile alternative to the system PC by which the MFS service software is usually controlled.
Whereas the system PC remains permanently installed and connected to a single eBOX in the system, the small, light operating panel is mobile and can be used flexibly for multiple eBOX devices, by plug & play via a CAN bus interface.
Furnished with a Windows panel PC, the MF-Control has a fine and precise touchscreen. With it, the full extent of the MFS service software can be used. In addition to the familiar functions such as process monitoring and fault analysis, further features that make the work of the user much easier are available via the operating panel.
All the eBOX devices used can be managed with the MF-Control. It is possible simply to change process parameters in job mode or to create new jobs in offline mode then to load them to the respective eBOX when a connection exists.
The MF-Control operating panel is therefore a helpful component of any servicing and maintenance department.