Nachi
Nachi GMS450 Skiving Machining Center For Gears
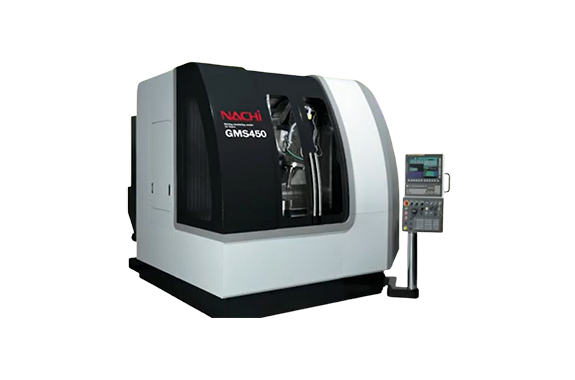
Manufacturer: Nachi-fujikoshi corp
Model: GMS450
Outline
Super accurate high performance skiving at peak of ideals
High efficiency gear skiving reduces machining time to as much as 1/5 (compared to gear shaping)
Proprietary technologies used to add lathe and drill to skiving machine for a multi-functional gear shaper
Both mass production & multi-type-small-lot production
Compact yet can be machining up to 450mm diameter part
Hard-skiving achieves high-precision machining of hardened gears
Interactive operation screen provides excellent man-machine interface
Features
Reduces machining time to as much as 1/5 (compared to gear shaping)
Three jobs consolidated in one machine
Skiving machining center for Gears GMS450 achieves a high-efficiency gear skiving machine. Plus. it also has lathe and drill functions that integrate jobs in this skiving gear shaping machine.To achieve smart production lines by reducing floor space
Skiving machining center for Gears requires little space to improve gear production lines to be smart production lines that can handle a variety of production formats from multi-type small-lot production to high-volume production.
Proprietary technologies produce new design skiving machine
Upright machining center built with gantry-type column Skiving machine with table that rotates on B-axis
New spindle designed for skiving
All axes have V-rail slides
Super-rigid spindle equipped with large diameter bearing and high-torque direct drive motor
V-rail slides with superior rigidity and damping used on all sliding surfaces. including the tool spindle.
X axis and B axis equipped with table clamp mechanism
Superior workability and operabilitySimple changeover and loading & unloading of workpieces
Easy access to Jig
Machining applicationSkiving cutter
Propose our skiving cutter and cutting conditions to match the various workpiece specifications and applications.
Features of NACHI cutters
Analyzed cutting mechanism with the cutting tool design technology and gear cutting technology that we have developed. Improved precision of machining work and extended tool life.
Established surface processing technology needed for skiving that produces better surfaces with optimized deposition process and design of coating components.
Carbide skiving cutters are able to achieve hard skiving process after heat treatment.
Learn more Skiving cutter
Conbination with NACHI robots
NACHI robots combine with machining . washing. deburring. and inspection equipment to produce a fully automated process.
NACHI Robots product lineup
Specification
Machining capacity | Max. workpiece diameter | mm | Ø450 |
---|---|---|---|
Max. machining module | — | m4.5 | |
Max. machining teeth width | mm | 120 | |
Max. workpiece height | mm | 250 | |
Gear cutting tool | — | Skiving cutter | |
Cutter spindle | Spindle taper hole (tool shank type) | — | 7/24 Taper No.50 (BBT50) |
Max. RPM of spindle | min⁻¹ | 3000 | |
Motor (30 min/continuous) | kW | 26 / 22 | |
Workpiece spindle | Max. RPM of spindle | min⁻¹ | 1400 |
Motor (30 min/continuous) | kW | 26 / 22 | |
Each unit traverse | Left–Right traverse (X-axis) | mm | 700 |
Forward–Back traverse (Y-axis) | mm | 350 | |
Up–Down traverse (Z-axis) | mm | 300 | |
Tool swivel angle (B-axis) | deg | ±25 | |
A.T.C. | Number of tool storage | piece | 6 |
Max. tool diameter | mm | Ø150 | |
Max. tool length | mm | 250 | |
Tool selection method | — | Tool storage position fixed / random | |
NC device | Type | — | FANUC 31i-B |
Display | — | FANUC PANEL-i | |
Utilities | Overall power used | kVA | 88 |
Dimensions of machine | Machine height | mm | 2700 |
Required floor space (width × depth) | mm | 2500 × 3860 | |
Net machine weight (main body) | kg | 22000 | |
Options | Workpiece chuck, External scale, 22 piece ATC, Hard machining package, Workpiece handling by robots |
Layout diagramProduct line-up for ring gear machining
GMS200 Main specification
Related Products
-
NACHI SS Series Wet Type Solenoid Operated Directional Control Valve (G01)
-
Nachi AQUA EX 3 Drill Flutes Hard
-
Nachi GSX MILL Ball Carbide End Mills
-
Nachi High Response Proportional Flow and Directional Control Valve
-
Nachi GSX MILL VL Long Shank
-
NACHI SCW Series Solenoid Valve with Monitoring Switch (SCW-G03)