Japan, Nachi
Nachi Load Sensing Valve
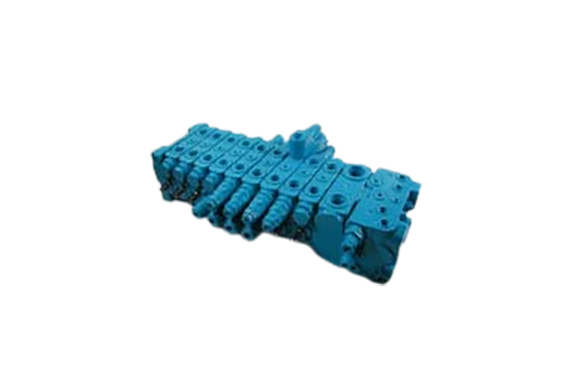
Made in: Japan
Manufacturer: NACHI
Model: Load Sensing Valve
Features
Provides all functions required for mini excavator
- Anti-saturation function
- Pressure compensation function according to self loaded pressure
- Cooperative system with engine speed
- No need for independent pump of swing motor
- LS control + constant horsepower control
- Good for straight traveling of wheel motors
- Various kinds of attached valves
Perfomance
1. Characteristics of pressure compensation
2. Characteristics of anti-saturation function
When supply flow is sufficient:![]() | When supply flow is insufficient:![]() |
- Same secondary pressure is supplied to every compensator
- Supply flow for all actuators is distributed in proportion to spool stroke.
3. Interconnected control stroke for engine rotation speed – Characteristics of flow
Normal load sensing system![]() | Cooperative system with engine speed![]() |
Target LS differential pressure is cooperative with engine speed
Much finer control with gentle gain between stroke and flow rate.
Application
- Ideal for construction equipment such as mini excavator
- If you use this unit in a set with our company’s PVK series load sensing variable piston pump the unit contributes to energy saving in the mother machine through load sensing control.
Specifications
Valve size | T04 (A/B port) | |
---|---|---|
Maximum working pressure (pump port) | 25MPa | |
Maximum working pressure actuator port | 28MPa | |
Maximum pump flow | 120 L/min | |
Maximum control flow (1 function) | 90 L/min | |
Tank port allowable back pressure | 0.3 MPa (1.5 MPa at peak) | |
Internal leakage (A/B port) | 5cm2/min at 5MPa | |
Internal leakage (boom lock valve) | 1cm2/min at 5MPa | |
Operating method | * Hydraulic pilot | |
* Manual | ||
* Electromagnetic proportional valve | ||
Structure of attached valves (Can be built-in) | * Overload relief | |
* Vacuum check valve | ||
* Boom lock valve (anti-drift valve) | ||
* Safety lock valve | ||
* Very slow-speed mode | ||
Applicable mini excavator (example) | 3 – 5-ton | |
Operating conditions | Hydraulic oil | ISOVG 32 to 68 |
Oil temperature (for common use) | -20 to 100°C(5 to 80°C) | |
Viscosity | 10 to 1000mm2/s | |
Ambient temperature | -20 to 60°C |
Operational theory
1. Secondary pressure feedback system with reducing valve
2. Self-load pressure-dependent pressure compensating valve
![]() | A2=A3=A , k=A/A1 PIN ![]() ![]() ![]() ![]() ![]() PL : Loaded pressure PLS : Secondary pressure through regulator Valve(=P-PLmax) PLmax : Maximum loaded pressure k : Area ratio |
Measurement
Related Products
-
Hammer Caster 429E-LB Big Size Elastomer
-
TSURUMI PUMP PARTS: PAN SCREW M4X115 SS (30L) Parts & Accessories
-
Vessel No.GT-P6T Air Impact Wrench, Torque Control Type
-
Daitoukeiki CP-4 Reference Liquid Column Pressure Guage
-
Chino CPA-L Fixed Mount Type Thermal Image Measuring Device
-
Showa Measuring Instruments RCT-580 Special Transducers