Gore (日本ゴア)
GORE Abrasion Resistant Cable Jacket for Civil Aircraft
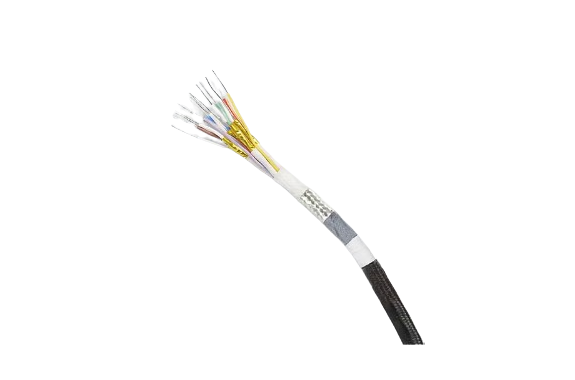
Manufacturer: Gore (日本ゴア)
Made in Japan
Model: Abrasion Resistant Cable
Overview of Abrasion Resistant Cable
Proven Superior Durability
The aerospace industry now requires high-speed copper cables installed in aircraft to meet new, more stringent durability standards. But, adding more durability to cable materials often includes thicker, heavier materials that can weigh aircraft down. Plus, bulky cables can be stiff, inflexible, and hard to route in small spaces as aircraft are being updated with more high-tech avionics.
Engineered with a revolutionary fluoropolymer fiber material, GORE Abrasion Resistant Cable Jacket is proven to meet new stricter industry standards for durability without sacrificing size, weight, or electrical performance. Our rugged jacket is resistant to abrasion and meets EN3475-503 requirements. You no longer have to use additional protective sleeving now required for high data rate copper cables installed in cockpit and cabin seats.
Using SAE AS4373™, method 703, we also compared 100-ohm quadrax cables packaged with four different jacket types, and the results were undeniable! Our abrasion-resistant cable jacket drastically outperformed PFA and FEP materials for superior cut-through resistance at high temperatures.
Cut-Through Resistant at High Temperatures
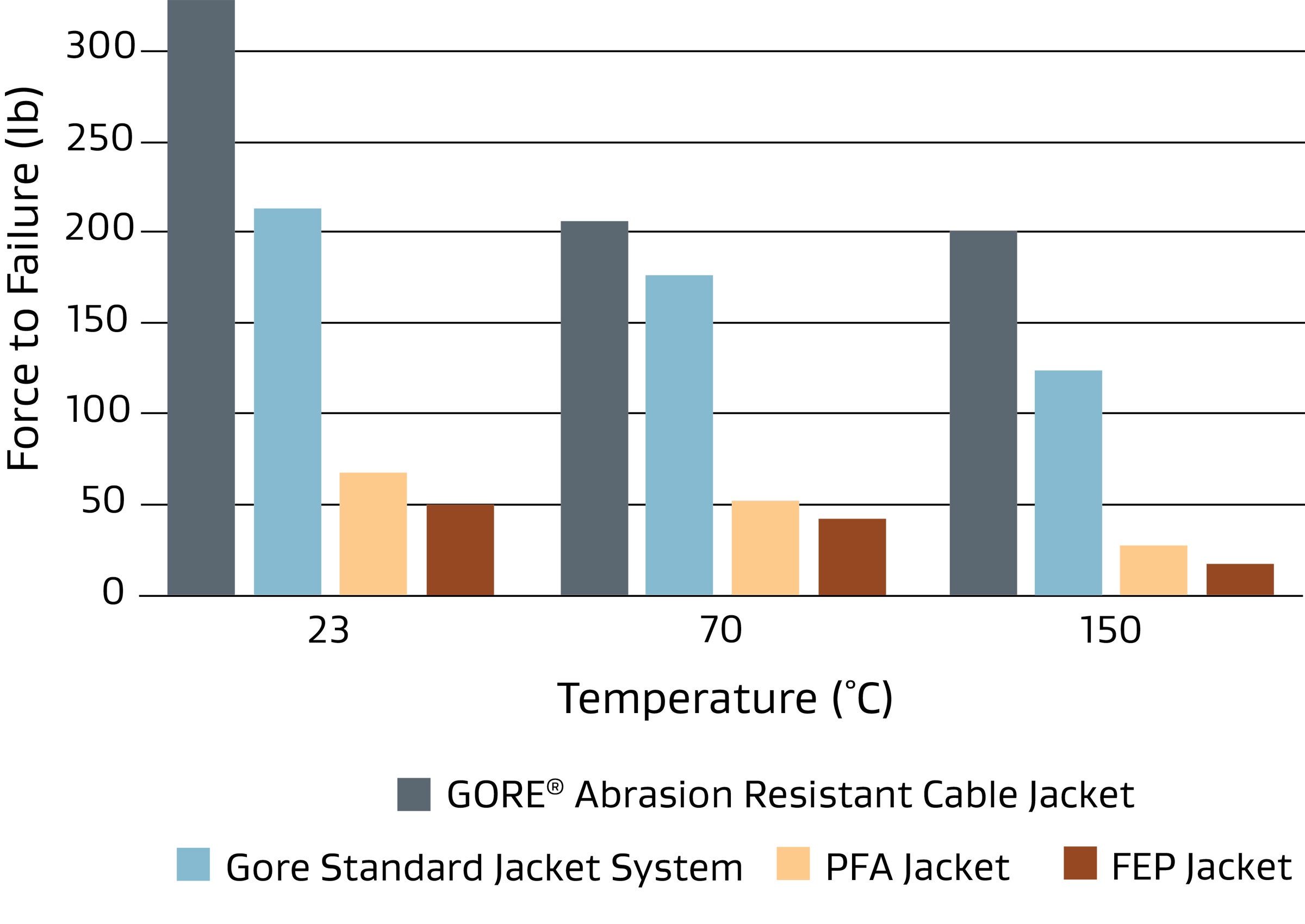
Thinner. Lighter Weight. More Flexible.
Another bonus is that our state-of-the-art cable technology is thinner, lighter, and more flexible with tighter bendability than alternative materials for improved installation in narrow seat configurations. Routing copper cables packaged with our abrasion-resistant cable jacket will be much easier and faster for maintainers. Despite installation complexities and extreme flight conditions, our jacket won’t crack, split or break.
Features & Benefits
Outperforming common industry materials, GORE Abrasion Resistant Cable Jacket offers added features for packaging copper wires, including:
- revolutionary fluoropolymer material
- resistant to abrasion, cut-through and high temps
- chemically inert material
- highly flexible, thinner, lighter construction
Our pioneering cable Jacket provides more benefits to system architects and engineers for best-in-class protection against typical aircraft conditions, like:
- meets stricter EN3475 and SAE AS4373™ durability requirements
- superior resistance against abrasion, high temperatures and more
- eliminates protective sleeving required for copper cables
- reliably transmits high-speed data and video
- expedited installation with more flexibility and tighter bending
- contributes to valuable aircraft weight savings
- ideal for wrapping GORE® High Speed Data Cables or alternatives
Technical Specs
These values demonstrate the electrical, mechanical and environmental performance of GORE® HDMI Cables, 2.0 version packaged with GORE Abrasion Resistant Cable Jacket for civil aircraft. Download our data sheet for more cable characteristics, qualifications and part number.
Elec./Mech./Environ. Property | Value |
---|---|
Signal Transmission Speed Gb/s | Up to 18 |
Standard Impedance Ohms | 100 ± 10 |
Typical Operating Voltage V | < 15 |
Nominal Velocity of Propagation % | 80 |
Nominal Time Delay ns/m (ns/ft.) | 4.10 (1.25) |
Capacitance pF/m (pF/ft.) | 230.0 (70.0) |
Maximum Skew Within Pair ps/m (ps/ft.) | 15.0 (4.6) |
Dielectric Withstanding Voltage Vrms Conductor-to-Conductor Conductor-to-Shield | 1500 1000 |
Jacket Material | Engineered Fluoropolymer Fiber Braid |
Jacket Color | Black |
Conductor | Silver-Plated Copper or SPC Alloy |
Conductor Color Coding | High-Speed Pairs: Blue/White, Brown/White, Green/White, Red/White Singles: Orange, Violet, White, Yellow Triad: Gray, Pink, Tan |
Dielectric Material | Expanded PTFE/PTFE |
Cut-Through Resistance kg (lb) (SAE AS4373™-703) 23°C 70°C 150°C | 122 (270) 73 (160) 59 (130) |
Scrape Abrasion Resistance Cycles (EN3475-503) 30°C & 55°C / F = 1.2 daN | > 8,000 |
Temperature Range °C | -65 to +200 |
Related Products
-
GORE Shielded Twisted Pair Cables for Defense Air & Land
-
GORE GTS Series For Smaller Spaces IDC Ribbon Cables
-
GORE Aerogel Insulation for Better Thermal Protection
-
GORE High Flex Flat Cables for Semiconductor Production Equipment
-
GORE Ethernet Cables For Civil Aircraft
-
GORE Dioxin and Furan Catalytic Filter Bags