Gore (日本ゴア)
GORE Dioxin and Furan Catalytic Filter Bags
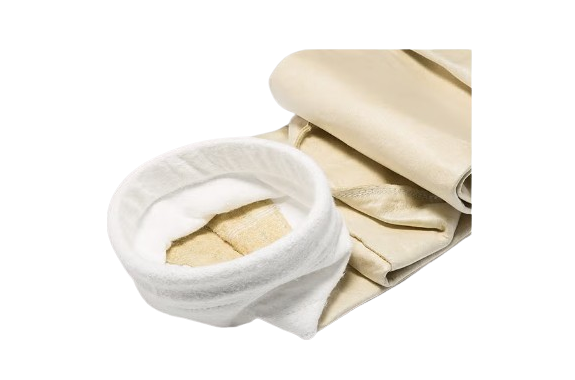
Manufacturer: Gore (日本ゴア)
Made in Japan
Model: Catalytic Filter Bags
Overview of Catalytic Filter Bags
Meeting the Dioxin Challenge
The threat of dioxins is drawing increasing attention around the world. Governments are phasing in tougher dioxin restrictions, and reports about dioxin levels in food products have generated widespread concern. Issues related to dioxin emissions and disposal are moving up the environmental agenda. With heightened public awareness, stricter regulations and potential penalties for non-compliance, it’s more important than ever to avoid the risks associated with inadequate dioxin control.
Eliminating Dioxins
GORE REMEDIA Filter Bags help you efficiently meet dioxin and furan emissions requirements without the burden of costly new equipment – all you need to do is install new filter bags. These bags are specially developed to filter for dioxin and furan emissions, removing it from your gas stream safely and efficiently.
The innovative dioxin filter system is effective and cost-efficient. Safer for the environment, safer for employees, simpler to use.
GORE REMEDIA Catalytic Filter Bags offer substantial benefits over sorbent injection systems and other dioxin control technologies.
- Destroy gaseous dioxins.
Unlike sorbent based systems such as powdered activated carbon (PAC), GORE REMEDIA Filter Bags do not merely remove dioxin and furan molecules from the gas stream to the solid residue stream, they destroy them. They use a high-performing, state-of-the-art catalysts to assure long life and levels of destruction that in many cases exceed 99 percent. - Lowest Total Cost of Ownership.
By combining dioxin destruction and particulate control into one passive filter, GORE REMEDIA Filter Bags provide low total cost of ownership. Made of catalyst/PTFE fibers, they have high mechanical strength and durability coupled with a proven long life catalyst, effectively assuring savings well into the future. Because it doesn’t add to your operating costs, there are no hidden costs after the system is purchased. - Lower disposal costs.
With no dioxin contaminated sorbents to dispose of, GORE REMEDIA Filter Bags minimize the cost of hazardous waste disposal. They address concerns about existing or future landfill restrictions on the amount and toxicity of sorbent levels in fly ash. Reducing hazardous waste disposal also demonstrates your company’s commitment to environmental protection. - No Need to Purchase New Equipment.
No new capital equipment is required. GORE REMEDIA Catalytic Filter Bags simply replace your current filters in your current baghouse so you can optimize your existing assets. In addition, no new equipment means there is no need to change your current process or add new maintenance requirements. - Passive System – No Maintenance.
Gore’s catalytic filter system is completely passive in operation, continuously destroying gaseous dioxins and furans while in operation. With no additional equipment to operate, ongoing maintenance demands are kept to a minimum. - Provide Dust Control.
The microporous structure of the GORE Membrane filters dust, even submicron particles. By capturing fine particles it reduces total emissions of toxins, such as trace heavy metals to the atmosphere. - Uses Existing Facility Footprint.
With no new equipment to buy, there are also no new demands on your existing facility footprint. Injection equipment, storage silos, catalytic towers, heat exchangers, etc., all require additional space and related construction. By utilizing your existing baghouse, GORE REMEDIA Filter Bags make compliance easy and affordable. - Reduce Corrosion.
The lower operating temperatures required with other dioxin control systems can cause corrosion in your baghouse. Since GORE REMEDIA Catalytic Filter Bags work at higher temperatures, there is less chance of corrosion. - Safer for Employees.
Carbon-based systems create a risk of baghouse fires. Hazardous carbon dust also puts operators at risk, especially when it is contaminated with dioxin. With GORE REMEDIA Filter Bags, avoiding carbon eliminates the risk of fires and minimizes potential health risks
Proven Technology
GORE REMEDIA Filter Bags represent state-of-the-art catalytic filter technology. They consist of a GORE Membrane (made of expanded polytetrafluoroethylene – ePTFE), laminated to a catalytic filter media – a specialist felt substrate. This catalytic media converts the dioxin and furan emissions, removing them from your gas stream in a highly innovative catalytic purification process.
Here’s how GORE REMEDIA Filter Bags work:
- The GORE Membrane captures fine particulate on the surface of the filter.
- As the filter is cleaned, solids are released from the surface and collected in the bottom of the baghouse hopper.
- The gaseous dioxins and furans pass through the Membrane into the catalytic filter media. The catalyst instantly reacts with the dioxin and furan molecules to convert them into insignificant amounts of CO2, H2O and HCl.
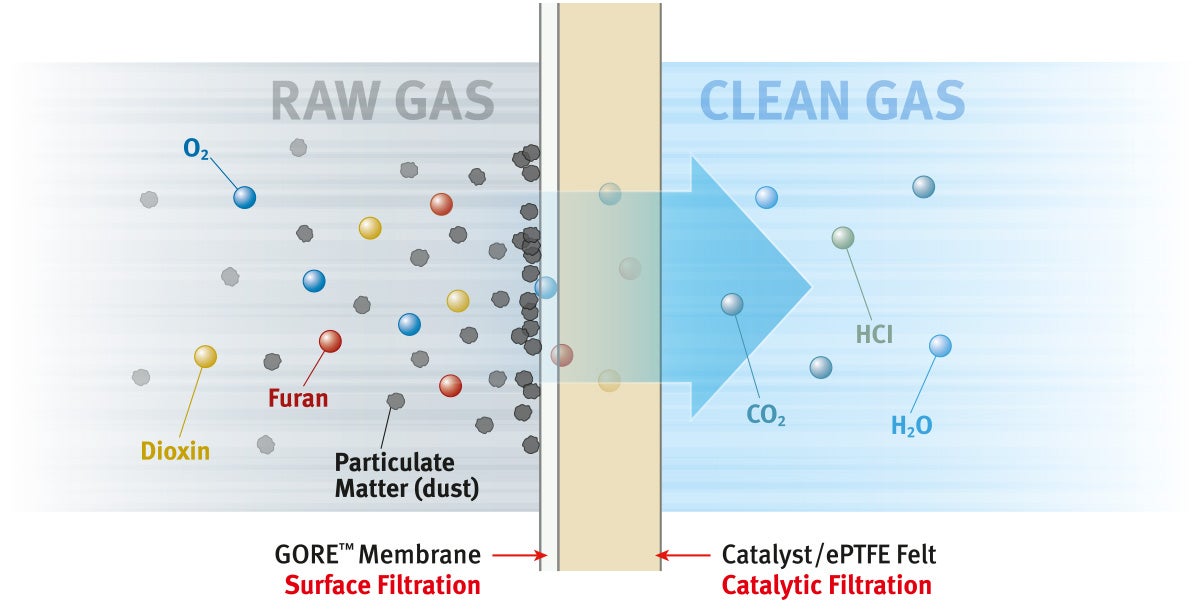
GORE REMEDIA Catalytic Filter Bags – Combining the principles of surface filtration and catalysis.
Combining the principles of surface filtration and catalytic filtration, GORE REMEDIA Filter Bags are a unique dioxin control alternative that works in your existing baghouse to destroy gaseous dioxins and furans to levels far below regulatory limits — safely, economically, and with minimal maintenance.
Incineration: Municipal, Hazardous & Medical Waste
The GORE REMEDIA Catalytic Filter Bags are installed in some of the world’s largest incinerators to simultaneously provide dust control and remove up to 99% of gaseous dioxin and furan emissions. Hazardous material filters must provide exceptional performance in order to meet the very low limits required – and our catalyst filtration system has proven to be up to the challenge.
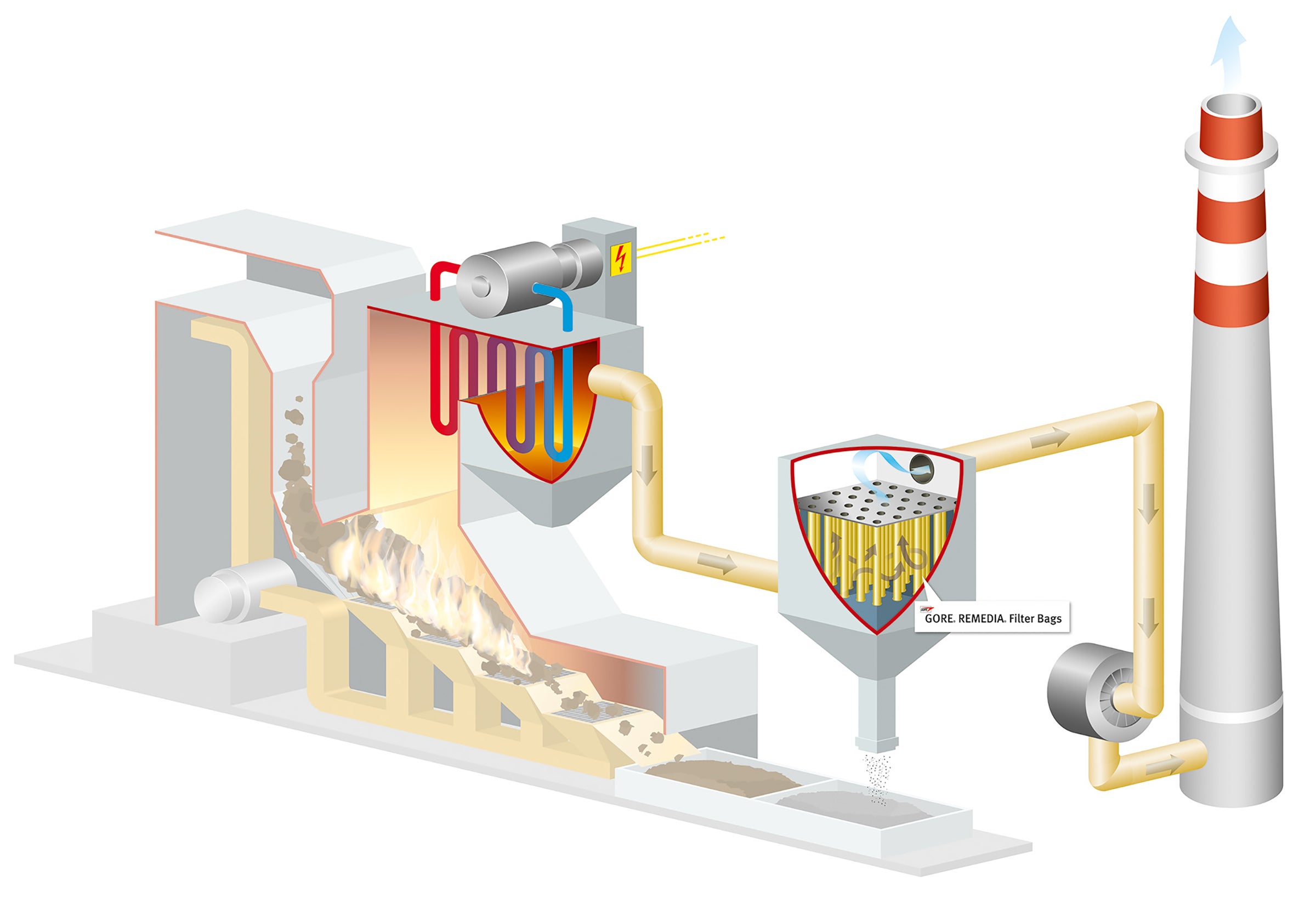
GORE REMEDIA Filter Bags work in your existing baghouse, without process modifications or changes to your physical plant.
In a variety of installations globally (municipal waste incinerators, hazardous, medical and industrial waste, crematoriums and pyrometallurgical plants) the GORE REMEDIA Catalytic Filter System yielded dioxin emissions at levels far below the standard guideline of 0.1 ng (TEQ)/Nm3. Furthermore, analysis revealed that the concentrations of dioxin in the fly ash using the GORE REMEDIA Catalytic Filter System were significantly lower than those achievable using a powder activated carbon (PAC) system.
Total dioxin and furan emissions to the environment, including release of both gas and solids from the baghouse, were reduced more than 90% compared to PAC systems – a fantastic achievement for our incinerator filter system.
At facilities operating under good combustion practices – a typical inlet dioxin concentration below 10 ng (TEQ)/Nm3 – the GORE REMEDIA Catalytic Filter System is designed to meet and exceed dioxin regulations.
If you need to reduce dioxin and furan emissions in your system and are interested in our catalytic filtration technology, get in touch with one of our specialists to discuss your application.
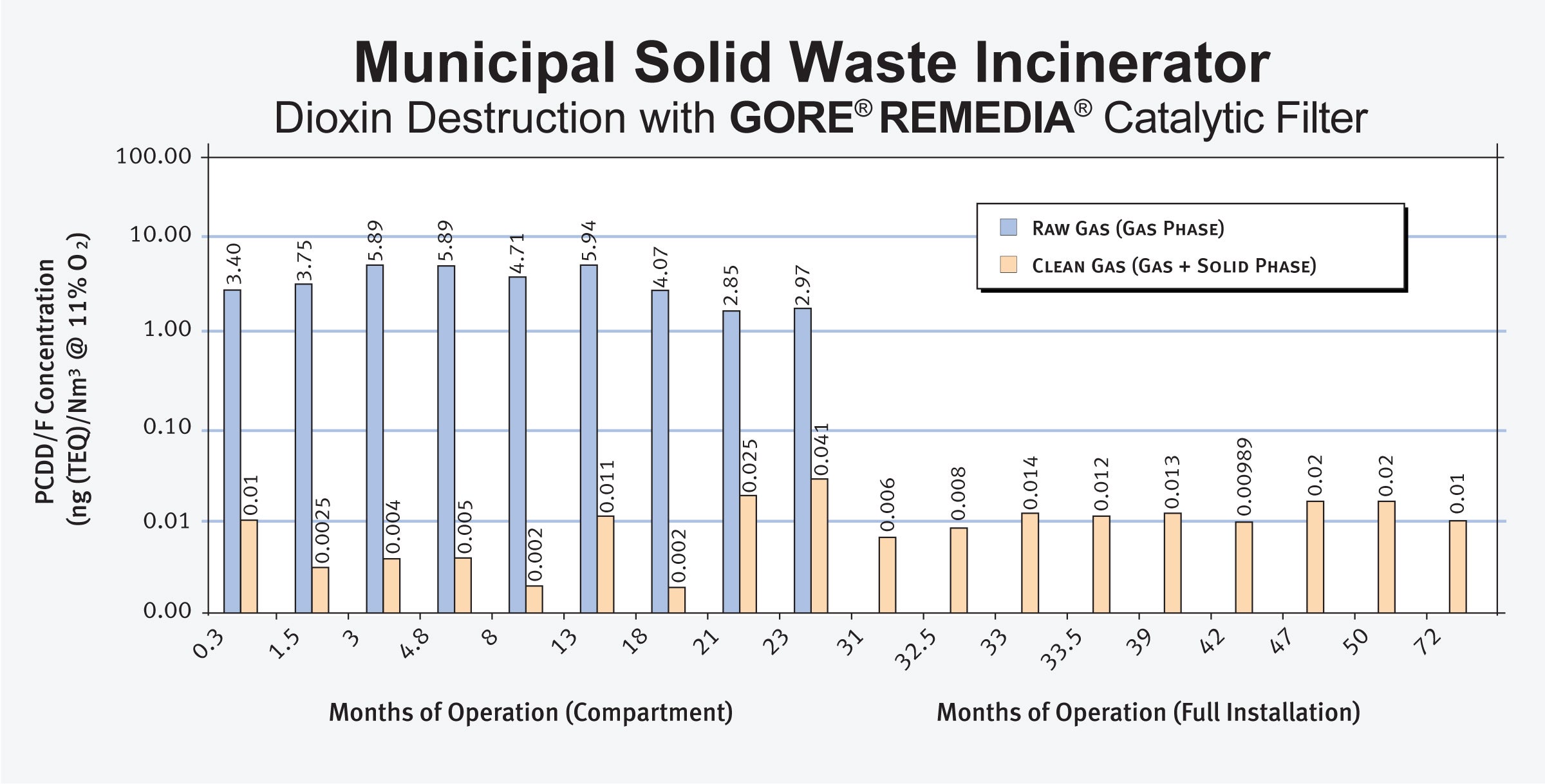
Technical Specifications
* All specifications are subject to change without notice
REMEDIA D/F CATALYTIC FILTER SYSTEM* | |
---|---|
Fiber content | Staple — GORE ePTFE Expanded PTFE/catalyst ePTFE Scrim Expanded PTFE fiber |
Felt construction | Supported needlefelt |
Membrane surface | GORE ePTFE |
Continuous operating temperature | 500ºF / 260ºC (maximum) |
Surge temperature | 525ºF / 274ºC (maximum) |
Acid resistance | Excellent |
Alkali resistance | Excellent |