Gore (日本ゴア)
GORE Filter Bags For The Cement Industry
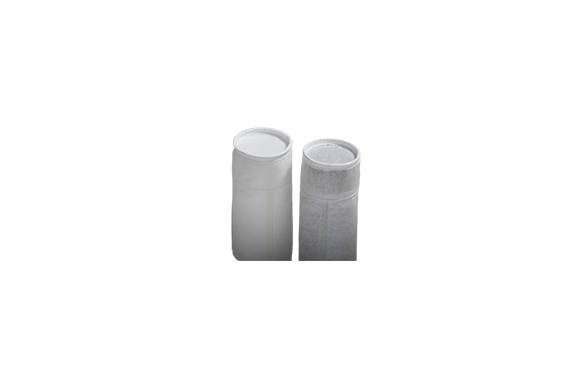
Manufacturer: Gore (日本ゴア)
Made in Japan
Model: Filter Bags
Overview of Filter Bags
Emissions control remains a critical issue in the cement industry. While cement plants prioritize throughput, failing to meet new NESHAP (National Emission Standards for Hazardous Air Pollutants) regulations can halt production immediately. This introduces significant cost implications that directly impact profitability.
Cement plants, especially baghouses, face challenges in compliance calculations. The MACT (Maximum Achievable Control Technology) approach establishes limits based on the top 12% of plants. Compliance is not evaluated at a single point in time but over a 30-day rolling average, making adherence more complex.
Before NESHAP, compliance required annual testing. However, the MACT standard sets new limits, reflecting the top-performing 12% of plants. Additionally, the rolling 30-day average increases the difficulty of maintaining compliance.
To address these challenges, cement producers globally trust GORE® Filter Bags. Designed for pulse jet and reverse air baghouses, these filter bags deliver reliable performance, ensuring uninterrupted operations while keeping plants continuously compliant. Gore’s filtration system includes lifetime technical support to optimize performance.
Advanced Filtration Technology by Gore
To meet the evolving needs of the industry, Gore introduced cutting-edge filtration solutions. These advancements enhance performance and reliability, helping cement plants meet emission standards while reducing operational costs. Key innovations include:
- GORE® LOW DRAG Filter Bags: These bags increase throughput while lowering dust collector costs.
- GORE® Low Emission Filter Bags: Seam-taped to block emissions and ensure compliance with NESHAP and similar regulations.
- GORE® DeNOx Catalytic Filter Bags: Capable of reducing NOx and NH3 levels like SCR towers but with significantly lower investment costs.
- GORE® Mercury Control System (GMCS): A fixed sorbent system that captures mercury and reduces SO2 concentrations in flue gas streams.
Key Factors in Filtration Selection
Baghouse operators evaluate filter bags based on three primary factors:
- Particulate Collection Performance
The filter must meet application requirements and ensure regulatory compliance. - Energy Costs
Lower resistance to flow (differential pressure) reduces energy usage. Increased resistance forces fans to work harder, raising energy consumption. - Filter Bag Longevity
Filters wear out due to holes or particulate buildup, leading to replacements. Long-lasting filter bags reduce maintenance needs and overall costs. Gore filter bags strike the perfect balance by offering:
- Exceptional filtration efficiency
- Minimal resistance to airflow
- Prolonged filter life
Typically, Gore’s filter bags last five years in a pulse jet cement kiln baghouse. Their durability ensures fewer replacements, minimizing maintenance costs, and improving productivity. Additionally, the lower pressure drop reduces energy consumption, cutting operational costs.
Reducing Total Cost of Ownership
GORE LOW DRAG Filter Bags introduce a revolutionary membrane class, enabling cleaner surfaces and optimized baghouse filter designs. This innovation reduces differential pressure, allowing for increased airflow or decreased fan energy consumption. Cement plants benefit from lower operational costs and greater efficiency, making these filter bags a transformative solution for emissions control.
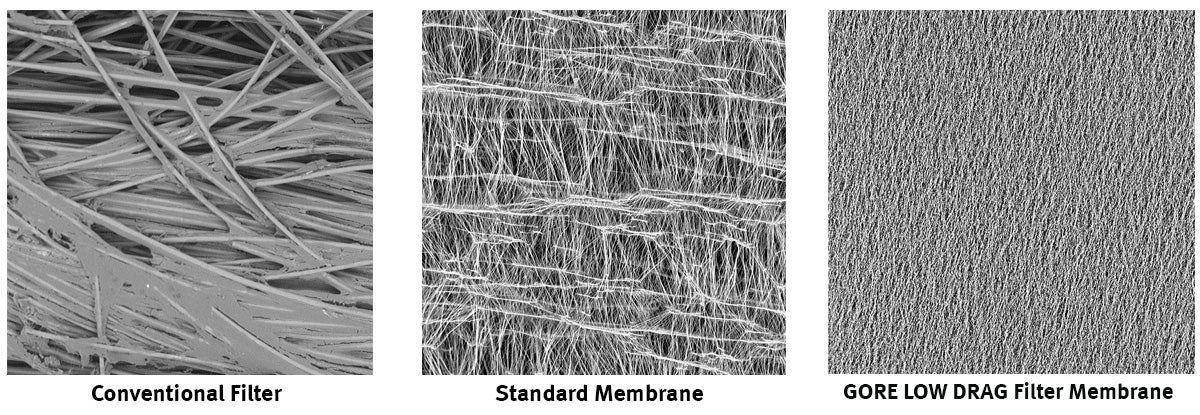

Cement producers can benefit from GORE LOW DRAG Filter Bags in multiple ways:
- Reduce fan energy costs
- Increase O2 availability in kiln
- Potentially increase use of alternative fuel
- Reliably meet emissions regulations
- Lowering total cost of ownership
Check out these scenarios:
Scenario 1 | Production is limited by airflow constraints through the kiln? Increase airflow and use this additional airflow for higher clinker production rates. |
Scenario 2 | Burning alternative fuels and limited by the amount of fuel burnt due to a shortage of available O2? Increase airflow and utilize this airflow to increase alternative fuel utilization. |
Scenario 3: | Can’t utilize additional airflow for production increases or alternative fuel increases? Reap the benefit of significant fan energy savings. |
Scenario 4 | Problem spots in the baghouse due to localized failures or abrasion? Permanently remove filter bags from these areas of the baghouse, while increasing performance. |
Controlling particulate emissions
Though each of our standard filter bags is proven to capture up to 99.99% of emissions, we have a new product especially effective at helping cement plants comply with NESHAP.
GORE Low Emission Filter Bags are especially designed for dust control in the cement industry. They have a PTFE-based seam tape ideal for cement dust control measures, as it makes it virtually impossible for dust to leak through the stitch holes. Studies show that dust emissions from the cement industry spike with each pulse of your cleaning system. GORE Low Emission Filter Bags don’t let dust through despite the constant pulsing — eliminating those emissions spikes, reducing your baseline emission level, and even extending bag life.
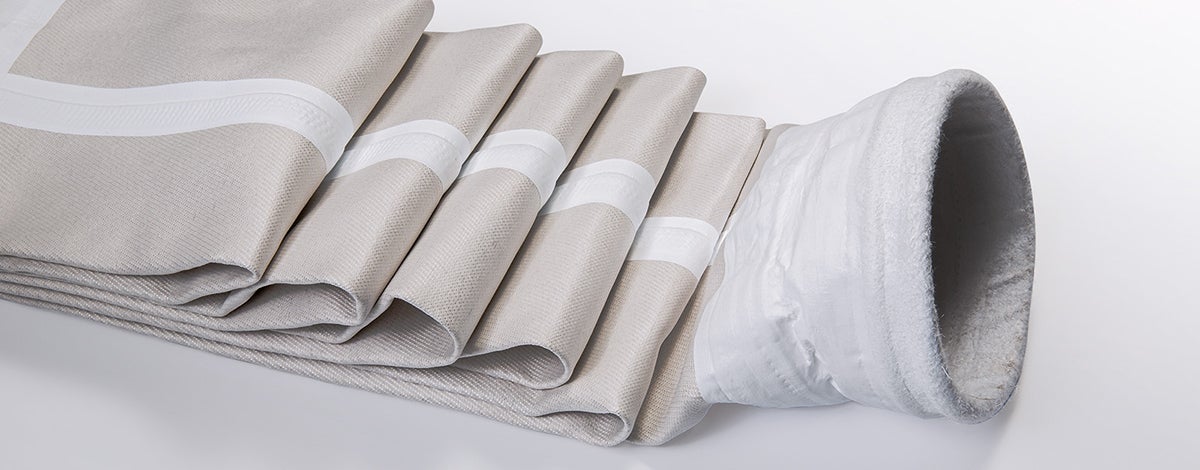
GORE Low Emission Filter Bags have a PTFE-based seam tape that makes it virtually impossible for dust to leak through the stitch holes. Gore’s new seam tape does not crack or split.
As the industry has evolved, other industrial filter bags have adopted membrane-based seam tape on their filters and technologies for cement dust control — but the Gore membrane remains ahead of the curve. Other seam tapes tend to crack and split during pulsing, eventually exposing stitch hole leak paths after 12–18 months. Our proprietary membrane remains mechanically robust, keeping emissions under control for the life of your cement filter bags while increasing your total amount of dust collection.
Controlling NOx
In some areas of the world, cement producers must also follow regulations for the control of NOx. To meet these regulations, we recommend GORE DeNOx Catalytic Filter Bags, which are specifically designed to destroy NOx and NH3.
These bags allow plants to achieve NOx and NH3 levels similar to an SCR tower, but at a much lower investment cost. They combine an outer-layer filter bag for particulate removal with a catalyst insert for NOx and NH3 reduction. And there’s very little installation or maintenance involved — in most cases, you just need to replace your current filter bags with GORE DeNOx Filter Bags.
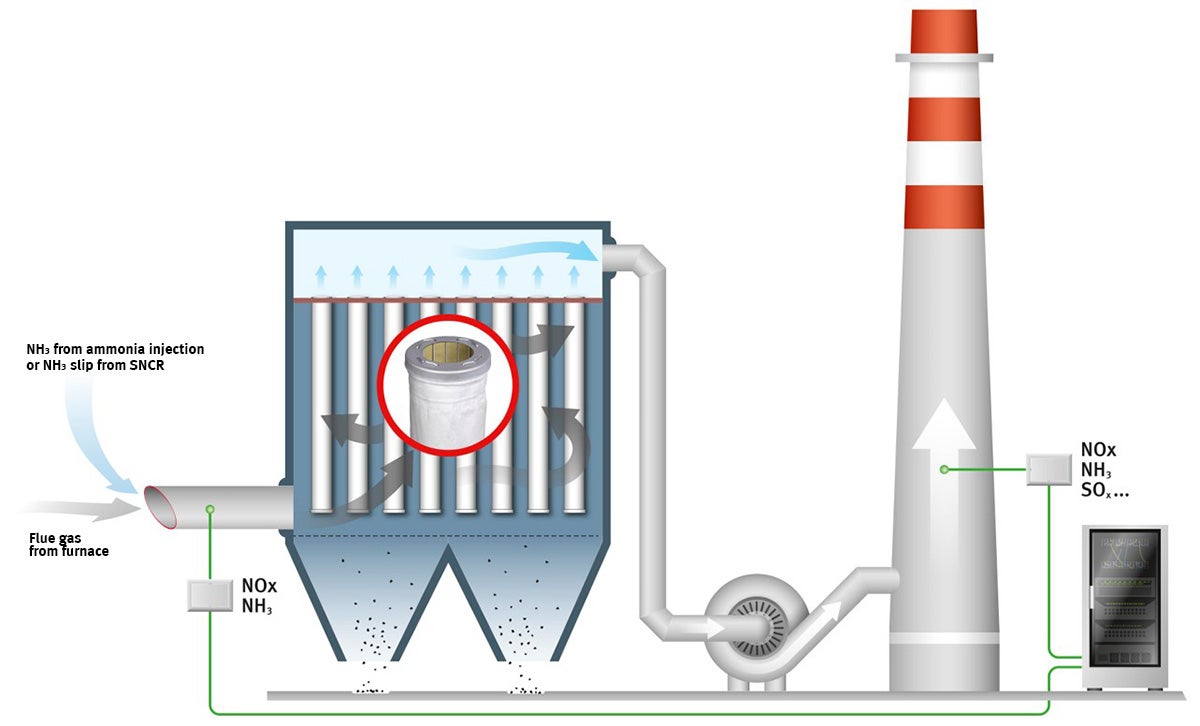
GORE DeNOx Catalytic Filter Bags can be easily installed and implemented just by replacing your filters.
Mercury Capture
Based on a novel Sorbent Polymer Composite (SPC) material, the GORE Mercury Control System provides both high efficiency and a high capacity for removing elemental and oxidized mercury from flue gas streams, and reduces SO2 concentrations.
There is no impact on the final product – the finished cement remains essentially mercury-free and carbon-free. By continually removing mercury from the process, it does not continually concentrate in the CKD. This eliminates the need for Dust Shuttling or Dust Wasting and their associated process changes. The kiln dust can be completely recycled back into the process to maximize clinker yield as is standard for the industry. There is also no need to worry about the logistics and safety of transporting and storing large amounts of powdered sorbents.
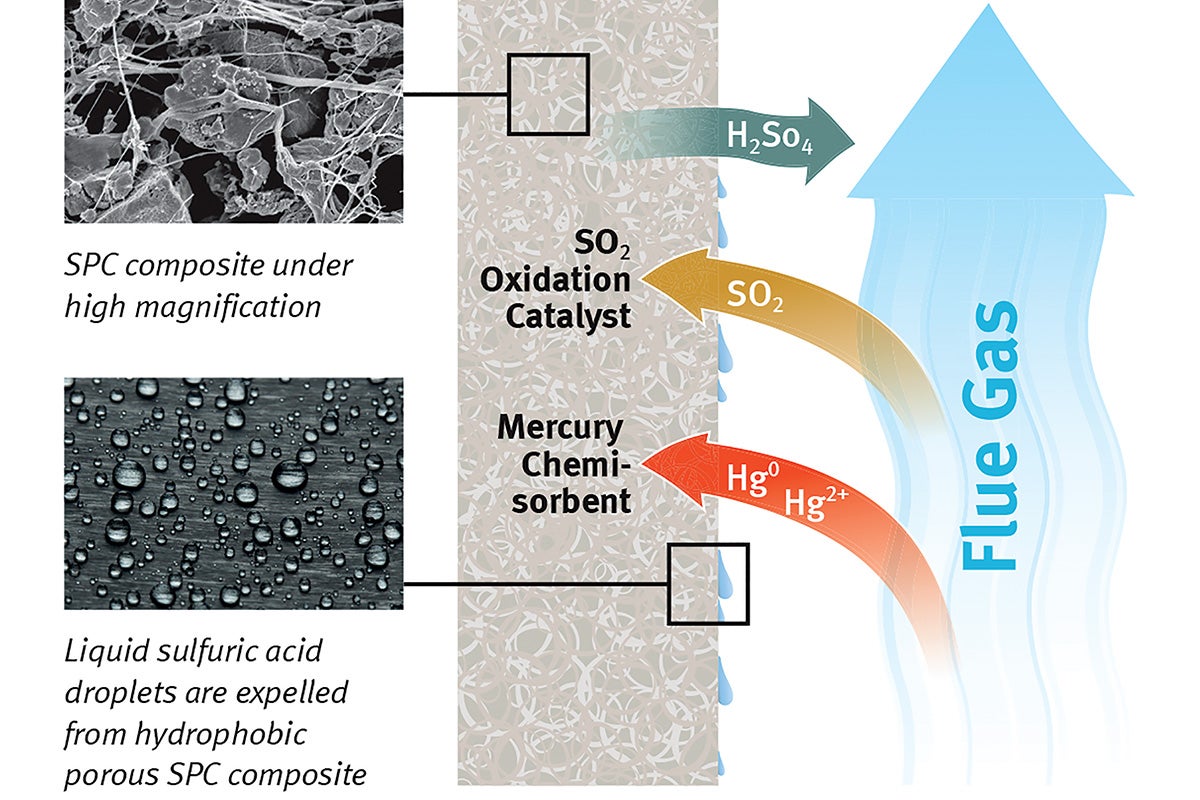
The SPC composite captures and sequesters elemental and oxidized mercury while converting SO2 to liquid sulfuric acid.
Why Choose Gore?
As a leader in developing high-quality filtration products for cement industry baghouses, Gore prioritizes customer needs and industry challenges. Our solutions address the real-world problems cement producers face daily, offering reliability and performance.
Gore pioneered PTFE-based membrane filters, revolutionizing filtration technology. These filters enhance airflow and capture up to 99.99% of harmful particulates, ensuring compliance with strict environmental regulations. Our PTFE membrane and robust construction guarantee both high performance and long-term value for your plant.
Key Advantages of Gore Filtration Products
When considering Gore filtration solutions for your system, keep three essential factors in mind:
- Innovative Products
Our filters deliver unmatched filtration performance. - Proven Reliability
Gore products consistently exceed expectations in performance and longevity. - System Approach
We offer comprehensive support for the lifetime of your filter bags, ensuring optimal performance and minimal downtime.
Together, these advantages provide the lowest total cost of ownership in the industry.
Reliability You Can Trust
Gore’s reliability stems from decades of experience and the use of premium materials like ePTFE (expanded polytetrafluoroethylene). This material offers several benefits:
- Chemically inert properties
- Resistance to extreme temperatures
- Hydrophobic surface
- Exceptional mechanical toughness
As the first to develop membrane-based filters for cement baghouses, Gore has set the industry standard. Our membranes capture even the smallest particulates while maintaining high airflow rates, regardless of kiln fuel materials. This ensures consistent performance throughout the filter bag’s lifespan.
By designing durable, high-performance filters, Gore reduces maintenance costs, minimizes downtime, and lowers the total cost of ownership. Strict production and testing standards ensure that every filter bag meets — and exceeds — performance expectations for five years or more.
Gore’s System-Wide Approach
At Gore, we don’t just sell filter bags; we partner with you to maximize their effectiveness. Our system-wide approach ensures that every aspect of your baghouse operates optimally.
As part of this approach, we:
- Customize filter bag designs to fit your specific application and process
- Optimize total system performance through analysis and improvements
- Provide lifetime technical support and troubleshooting
This partnership ensures you achieve peak productivity while maintaining compliance. Even if your team lacks in-house filtration experts, Gore offers day-to-day troubleshooting to resolve any filter bag-related issues.
Evaluating the Total Cost of Filter Bags
The total cost of a filter bag involves more than the purchase price. You must also consider:
- Installation costs
- Maintenance and cleaning expenses
- Energy costs for baghouse fans
- Stack testing and monitoring fees
- Expected filter bag lifespan
GORE Filter Bags deliver the lowest cost of ownership by combining:
- Superior membrane laminates
- Robust bag construction
- Optimized system-wide performance
- Lifetime technical support
- Unmatched reliability
Success Stories: Real Results with Gore
Global Cement Producer
A major cement plant replaced two inefficient wet-process kilns with a single state-of-the-art preheater/precalciner kiln, boosting production from 1.7 million to 2.8 million tons annually. Alongside this upgrade, the plant installed a Fives TGT® baghouse equipped with GORE Low Emission Filter Bags. These seam-taped bags ensure compliance with NESHAP and NSPS regulations, enabling the plant to meet stringent emissions limits confidently.
Eco-Friendly Cement Plant
An environmentally progressive cement plant relies on GORE Filter Bags to meet aggressive emissions goals while reducing costs. A process engineer noted, “GORE Filter Bags allow us to meet environmental standards without sacrificing productivity.”
North American Construction Supplier
One of North America’s largest construction materials suppliers improved system performance with GORE Filter Bags. The bags optimized productivity, lowered operational costs, and met emissions targets. According to their director of engineering, “GORE Filter Bags allow us to keep up with production demands without additional capital investment.”
GORE Filter Bags: Designed for Compliance
GORE Low Emission Filter Bags ensure full compliance with NESHAP regulations. Their seam-taped construction prevents leaks, guaranteeing emissions remain below regulatory limits while maintaining exceptional durability.
For NOx control, GORE DeNOx Catalytic Filter Bags provide an efficient, cost-effective alternative to SCR towers. These filters destroy NOx and NH3 emissions while reducing installation and operating costs.