Japan, Kurimoto
Kurimoto Bending Roll
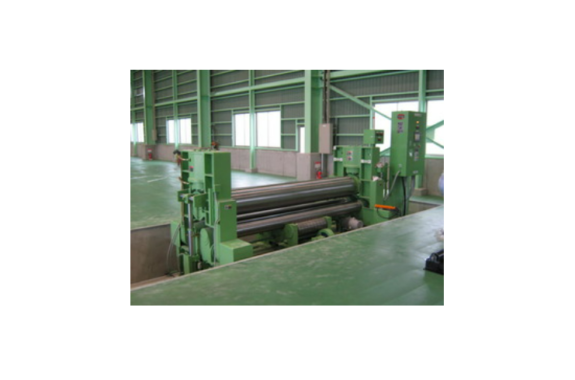
Product Made in Japan
Manufacturer: KURIMOTO
Kurimoto’s proven high-precision end bending features bring precise circularity to desired application.
KURIMOTO’s Bending Roll is Top Roll Horizontal Movement type. Value added features of KURIMOTO’s Bending Roll, such as Top Roll crowning and adjustable Back-Up Rolls enable to achieve precise circularity and cylindricality to application with wide range of material thickness
Features
NC Control
Amount of Top Roll Ram Down is automatically calculated by inputting application data, which reduces workers operation.
High-Precision End Bending
Being formed in the procedure that Top Roll moves Front/Rear direction, the ends of the material plate are firmly bended as well as the one done by ordinal press.
Precise Circularity and Cylindricality
Top Roll Crowning and adjustment of Back-Up Roll help correcting deflection of both Top Roll and Back-Up Rolls to be more precise circularity and cylindricality of applications, which reduces time of post procedure.
High Rigid Mechanical Structure
Frame is rigidly designed based on pressure capacity and width of application materials. Top Roll Ram- Down mechanism and rigid & compact lower frame simplify foundation construction.
Energy Saving and Eco-Friendly
While the unit is not loaded, inverter control minimizes pump unit motor output and reduces Electricity Consumption of pump unit motor.
User-Intuitive color touch panel
Achieves precise circularity and cylindricality to both large and small diameter application.
Application
Pressure Vessel (Compression tank) manufacturing
Heavy machine parts manufacturing
Ship and Ship Parts manufacturing
Stainless tank manufacturing
Specially equipped vehicle parts manufacturing
Bending Method
Conventional 4-Roll Bending Process
The Problem:
- Straight sections always remain at the leading and trailing edges of the rolled sheet.
- While an experienced machine operator can partially correct these straight sections, no machine yet has been able to eliminate them completely.
Kurimoto’s New 3-Roll Bending System
The Kurimoto’s sytem uses a top roll that changes position during the bending operation to produce leading and trailing edges formed to almost 100% perfect curves. The result? A rolled form with almost perfect concentricity – right down to the edges. How is it done? A computerized control system continually sets both the height and horizontal position of the top roll during the bending process. It’s all automatic, so anyone can operate the machine.
Concentricity check after bending shows almost 100% accuracy in the cross section of the curve.
Post processes after conventional 4-roll bending
Processes required after Kurimoto 3-Roll Bending:
Easy Operation
The computer-controlled Kurimoto system offers simple “one-touch” operation.
Just input the material type, thickness, width and product diameter.
No experience needed.
Anyone can operate the machine first time, any time.
Material
Plate Thickness
Plate Width
Product diameter
Optimum Bending
Precise and Highly Uniform Roll Formed Products
Kurimoto uses a high-strength backup roll that allows the system to form sheet metal of any thickness into perfectly straight cylindrical forms. Welding time is significantly shortened after rolling. | ![]() |
![]() | ![]() | ![]() | ![]() |
Thick plates are rolled into perfect cylinders. | Thin plates are rolled into perfect cylinders. |
Specifications
Achieves simplified operation
Proven NC Control system ensure precise bending result which used to heavily rely on worker’s experience and know-how, by inputting details of application.
Every workers can operate KURIMOTO Bending Roll easily by inputting material, thickness, width and inner diameter of application without particular work experience.
NC Control
Semi Automated type(TNC) is recommended for Various kind but low-volume production
Fully automated type(CNC) is recommended for Various kind with high-volume production
Top Roll travel and Ram-Down are automatically calculated by inputting details of application so unexperienced application can be processed easily in a short time.
Portable machine
Main cylinders for Top Roll are designed as to press down application, and reduce lower frame height so material loading height remains low.
Frame is rigidly designed so anchor bolts are not required to install machine.
M series pressure capacity 25~60 tons
MP series pressure capacity 75~430 tons
M series pressure capacity 490 tons
500 ~ 8,000mm width plate is available to offer.
Maximum plate thickness is calculated based on the yield point 255N/mm2 standard.
Capacity (x9.8kN) | Plate thickness (mm) | Plate width (mm) | Roll diameter (mm) | Bottom Roll Pitch (mm) | Electric Motor (kW) | ||||
End bending | Central bending | Top Roll | Bottom Roll | Drive | Hydraulic | Movement | |||
(MJ) 25 | 6 4.5 | 8 7 | 1500 2000 | 175 195 | 125 | 160 | 1.5 | 1.5 | Oil Hydraulic Motor |
30 | 6.5 5.5 | 8.5 7.5 | 1500 2000 | 185 205 | 125 | 160 | 1.5 | 1.5 | Oil Hydraulic Motor |
37 | 8 6 5.7 | 10 8 8 | 1500 2000 2500 | 205 220 235 | 135 | 180 | 2.2 | 1.5 | Oil Hydraulic Motor |
45 | 9 7.5 6.5 | 11 10 9 | 1500 2000 2500 | 215 235 245 | 135 | 180 | 2.2 | 1.5 | Oil Hydraulic Motor |
55 | 8 8 7 | 11 10 9.5 | 2000 2500 3000 | 245 255 275 | 145 | 200 | 3.7 | 2.2 | Oil Hydraulic Motor |
65 | 10 9 8 | 13 12 11 | 2000 2500 3000 | 250 265 280 | 145 | 200 | 3.7 | 2.2 | Oil Hydraulic Motor |
(MP) 75 | 12 10 9 | 15 14 12 | 2000 2500 3000 | 255 270 290 | 150 | 245 | 3.7 | 2.2 | 0.75 |
100 | 13 11 | 16 15 | 2500 3000 | 300 325 | 165 | 270 | 5.5 | 3.7 | 1.5 |
130 | 16 14 | 19 18 | 2500 3000 | 330 350 | 180 | 300 | 5.5 | 3.7 | 2.2 |
160 | 18 16 14 | 22 20 18 | 2500 3000 3500 | 360 375 390 | 200 | 330 | 7.5 | 5.5 | 2.2 |
190 | 21 19 16 | 26 22 19 | 2500 3000 3500 | 380 400 410 | 220 | 360 | 11 | 5.5 | 3.7 |
230 | 25 22 19 | 29 27 25 | 2500 3000 3500 | 410 425 440 | 235 | 380 | 15 | 7.5 | 3.7 |
270 | 28 25 22 20 | 33 30 28 25 | 2500 3000 3500 4000 | 430 450 470 490 | 250 | 400 | 15 | 7.5 | 3.7 |
320 | 30 28 25 22 | 36 32 30 28 | 2500 3000 3500 4000 | 460 480 500 520 | 260 | 420 | 18.5 | 7.5 | 5.5 |
380 | 35 32 28 25 | 39 35 32 30 | 2500 3000 3500 4000 | 500 510 530 550 | 275 | 460 | 22 | 11 | 5.5 |
430 | 40 35 32 30 | 43 40 40 36 | 2500 3000 3500 4000 | 520 540 560 580 | 290 | 500 | 30 | 11 | 5.5 |
Our machine can also be manufactured according to other than this specification. Contact us for more details.
We have satisfied result following case, plate width is 8m and plate thickness is 100mm.
This specification is subject to change without prior notice.
Related Products
-
Kansai Electric Heat Corp SHW Series Air Heater
-
Mikasa 16″MW-DA Concrete Cutter
-
Hammer Caster 935SMR Stainless Steel Caster
-
Japan Clamp WU Wheel Lifting Clamp
-
Ross Asia Crossflow 35 series Double valve, with or without pressure switch, ports 1/4 to 3/4
-
TONE TN-30E-1, TN-30E-2 Electronic Angle Control Wrench