Japan, Kurimoto
Kurimoto Continuous Rotary Type Through-flow Dryer
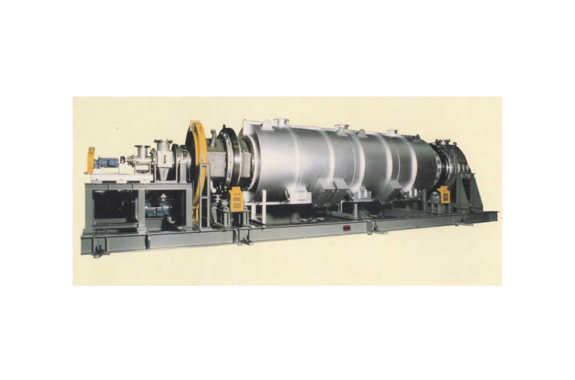
Product Made in Japan
Manufacturer: KURIMOTO
This dryer has double rotary shells consisting of a horizontal external shell and an inclined internal shell. The internal shell is comprised of numbers of vanes as shown in the figure. The annular section between the external and internal shells serves as a passage of the hot air and is divided into numbers of segments. The hot air is fed from this annular section through the gaps between the vanes and exhausted through the material layer, which continuously moves. The material is fed into the internal shell from the same direction as that at the hot air inlet and dried along with the shell rotation while continuously moving to the outlet.
Features
Large heat capacity coefficient and high heat efficiency
The hot air passes directly through the material layer to provide a maximum of touch area between the hot air and the material, allowing a large calorific value, Ua = 2,100 to 7,500 KJ/m3hr℃, which transfers from the hot air to the material.
Large hold-up available
It is possible to provide 15 to 20% of hold-up compared to 10% with other types of rotary dryers, making it possible to reduce the volume of the dryer.
Minimized material destruction
This dryer has no process to lift the materials up and down with a lifting wing, suppressing the destruction of the material particles.
Less wear of vanes
This dryer has no process to lift the materials up and down with a lifting wing, minimizing the wear of the vanes.
Minimized uneven drying
Superb mixing of materials is provided through the rotation and aeration, enabling you to get homogeneous products with uneven drying minimized.
Drying possible to low moisture content
Possible extended residence time (some for 3 hours) enables the materials to be dried up to extremely low moisture content.
A constant rate of hot air can be fed in the material layer.
Drying and cooling can be performed in a single unit.
Continuous, Rotary Type Through-flow Dryer
Summary
This dryer has double rotary shells consisting of a horizontal external shell and an inclined internal shell. The internal shell is comprised of numbers of vanes as shown in the figure. The annular section between the external and internal shells serves as a passage of the hot air and is divided into numbers of segments. The hot air is fed from this annular section through the gaps between the vanes and exhausted through the material layer, which continuously moves. The material is fed into the internal shell from the same direction as that at the hot air inlet and dried along with the shell rotation while continuously moving to the outlet.
Features
- Large heat capacity coefficient and high heat efficiency
The hot air passes directly through the material layer to provide a maximum of touch area between the hot air and the material, allowing a large calorific value, Ua = 2,100 to 7,500 KJ/m3hr℃, which transfers from the hot air to the material. - Large hold-up available
It is possible to provide 15 to 20% of hold-up compared to 10% with other types of rotary dryers, making it possible to reduce the volume of the dryer. - Minimized material destruction
This dryer has no process to lift the materials up and down with a lifting wing, suppressing the destruction of the material particles. - Less wear of vanes
This dryer has no process to lift the materials up and down with a lifting wing, minimizing the wear of the vanes. - Minimized uneven drying
Superb mixing of materials is provided through the rotation and aeration, enabling you to get homogeneous products with uneven drying minimized. - Drying possible to low moisture content
Possible extended residence time (some for 3 hours) enables the materials to be dried up to extremely low moisture content. - A constant rate of hot air can be fed in the material layer.
- Drying and cooling can be performed in a single unit.
Construction
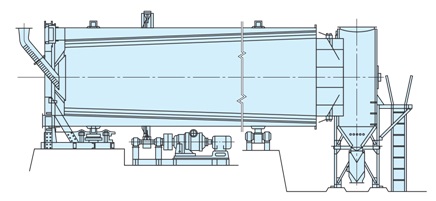
Application
Sugar, coke, and flat soybeans
Synthetic resin pellets
Wood chip and pulp waste
Coal and blast furnace slag