Japan, Orientalmotor
Orientalmotor AZ Series αSTEP
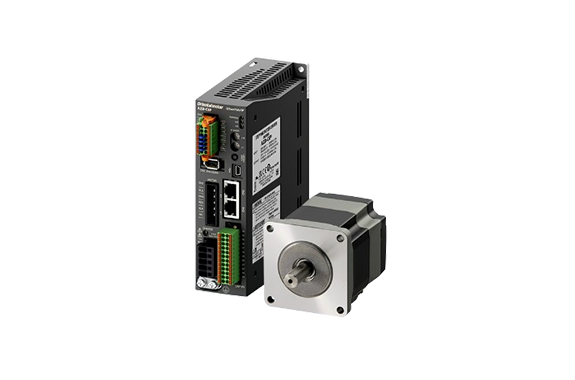
Made in Japan
Manufacturer: ORIENTAL MOTOR CO., LTD.
Model: AZ Series
Equipped with ABZO sensor
Newly developed ABZO sensor
This is a small, battery-less mechanical absolute sensor. It contributes to improving productivity and reducing costs.
Both the motor and driver come at a budget-friendly price, making them an economical choice. Additionally, this affordability does not compromise their quality or performance.
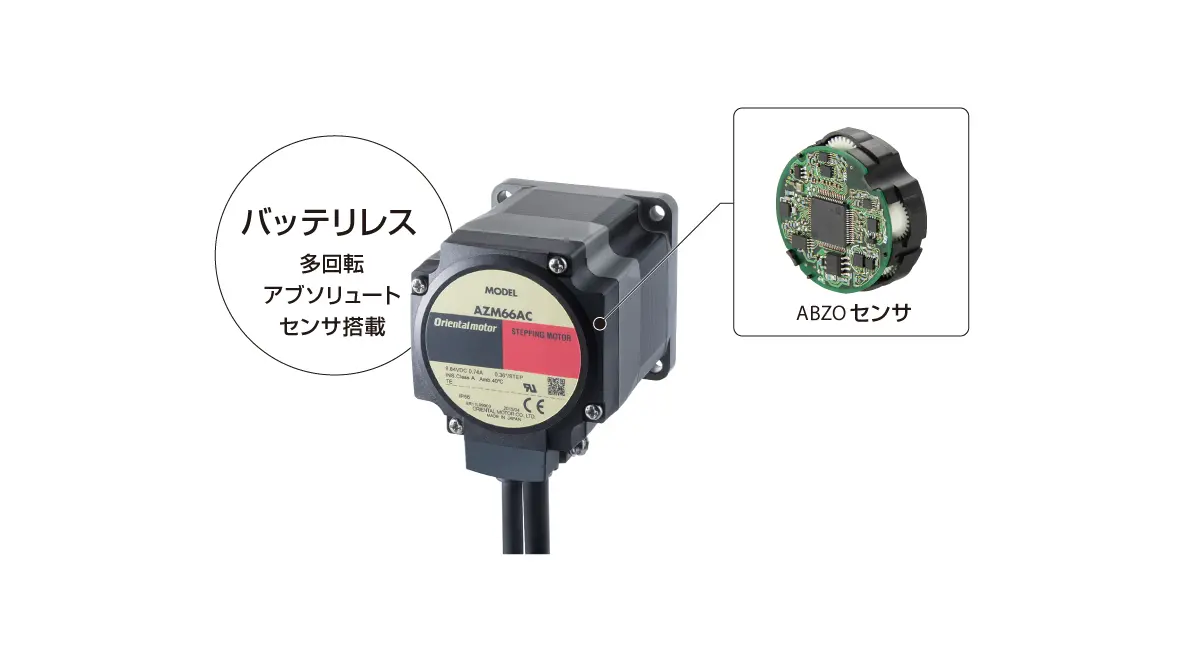
Mechanical Sensors
The ABZO sensor features multiple gears and detects position information by recognizing the angle of each gear.Consequently, it removes the necessity for a battery. Furthermore, this design guarantees uninterrupted operation and dependability without depending on external power sources.
Multi-rotation absolute sensor
Starting from the reference origin, the system can detect the absolute position of the motor shaft within a range of ±900 rotations, totaling 1800 rotations. This capability ensures precise monitoring and control over the motor’s position.
* Mounting dimensions 20mm, 28mm (30mm) are ±450 rotations (900 rotations).
No external sensor required
Since it is an absolute system, there is no need for external sensors like origin sensors and limit sensors. This design simplifies the setup and reduces the need for additional components.
High speed return to origin + Improved return to origin accuracy
Return to origin is possible without an origin sensor or limit sensor. The system achieves high-speed return to origin without concerns about sensor sensitivity, thereby shortening the machine cycle. This efficiency improvement enhances overall performance and productivity. At the same time, there is no longer any variation in the origin position due to sensor sensitivity. This improves the precision of the origin.
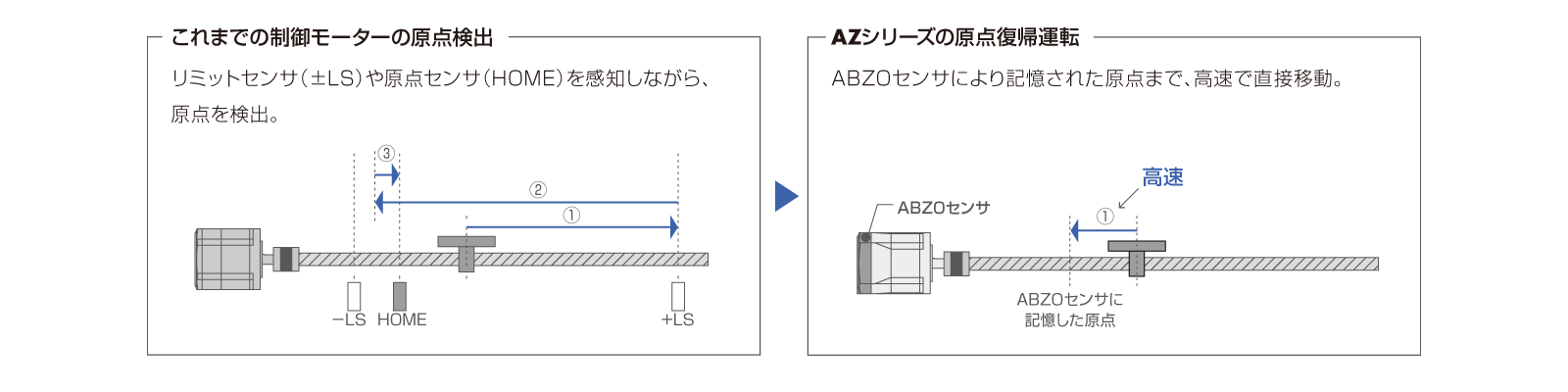
Cost reduction
There is no need to pay for external sensors or wiring, reducing the cost of the entire system.
Greater freedom in device design
This saves the space previously required for installing and wiring external sensors, and increases the freedom of device design.
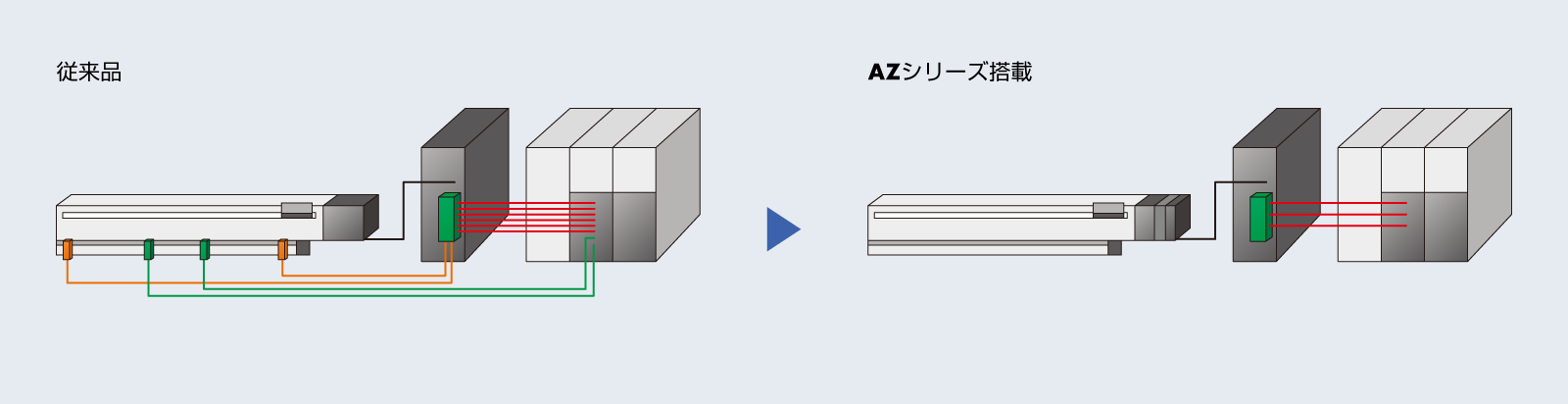
Not affected by external sensor malfunctions
There is no risk of external sensor malfunction, failure, or disconnection, which can occur in environments where metal chips are flying around during metal processing or where oil mist is present.
Battery-less
This mechanical sensor eliminates the need for a battery, as it manages position information through mechanical means. This design ensures continuous and reliable performance.
Hold location
If the power cuts off during positioning operation or the cable between the motor and driver disconnects, the system maintains the position information. This feature reduces the time needed for return-to-origin operation, ensuring efficiency and reliability.
Reduced maintenance
No need to replace batteries, reducing maintenance efforts and costs.
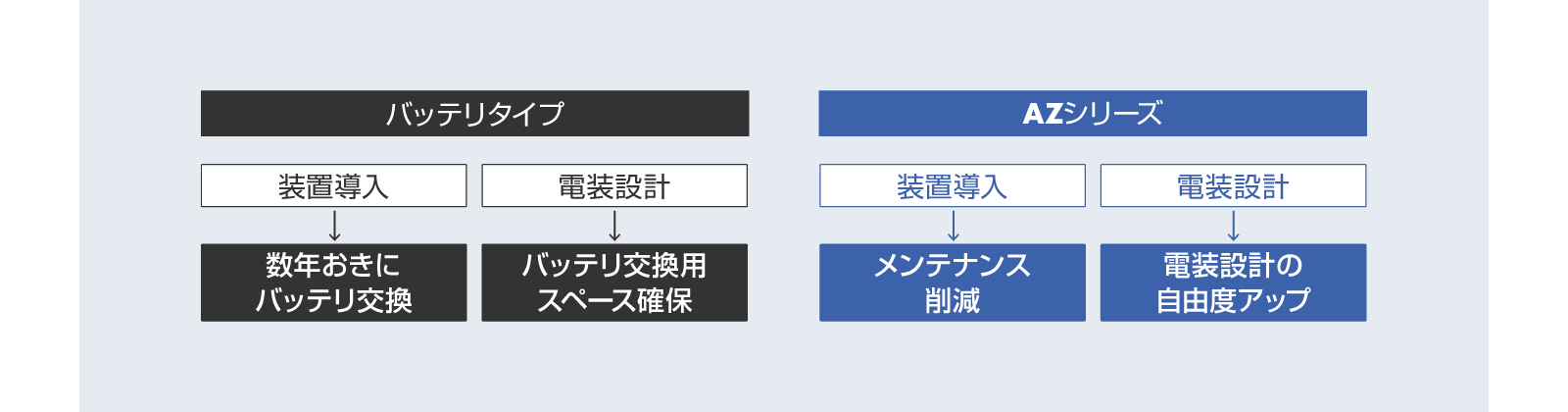
Greater freedom in driver installation
This saves the space previously required for battery installation and wiring. There are no restrictions on where the driver can be installed, improving the freedom of layout design for control panels, etc.
Reliable overseas shipping
Since batteries self-discharge, care must be taken when transporting equipment for long periods of time, such as when shipping overseas. With the ABZO sensor, there is no time limit for retaining position information. In addition, there is no need to consider various regulations when exporting batteries overseas.
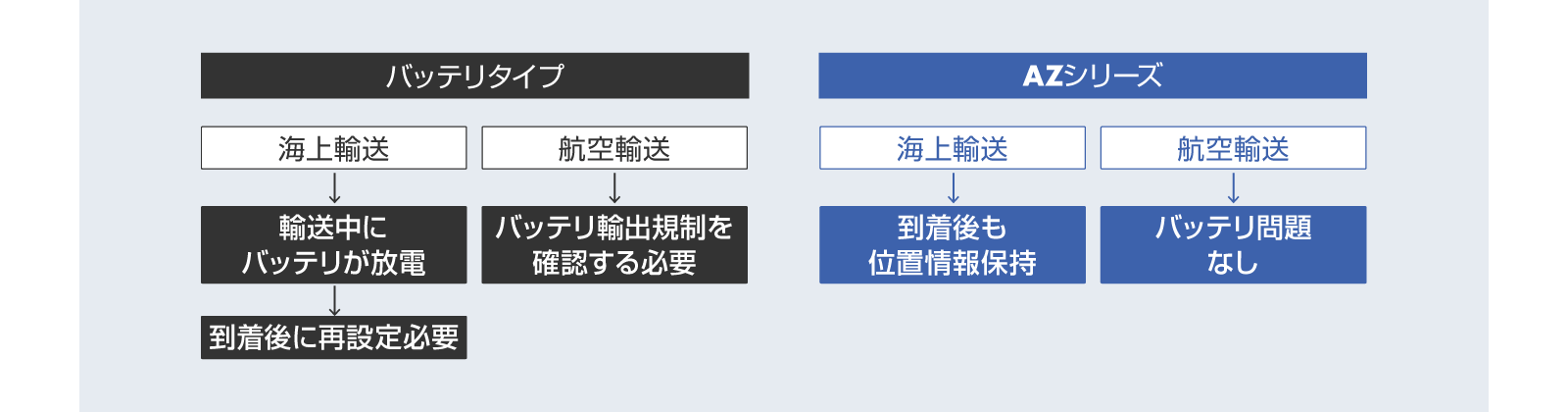
Low power consumption and low heat generation
Greatly reduces heat generation
Temperature distribution by thermography
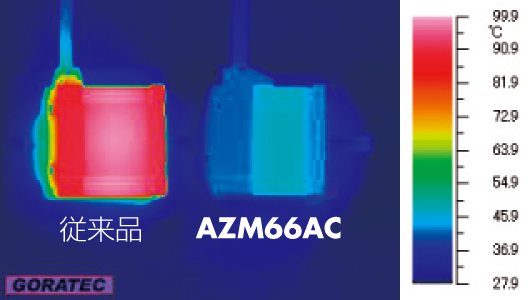
Motor housing temperature when operating under the same conditions
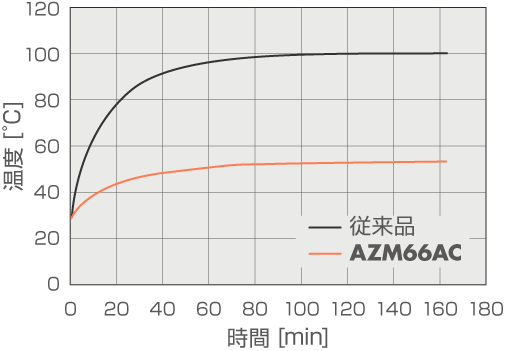
Energy saving reduces power consumption
AC power in
Power consumption and CO2 emissions reduced by 47% compared to previous models (compared to our previous models)
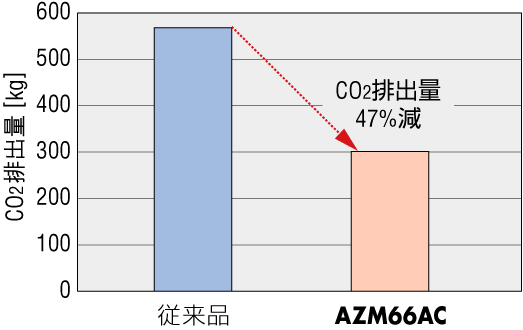
Operating conditions
Rotational speed | 1000r/min |
Load factor | 50% |
Operating time | 24-hour continuous operation, 365 days a year |
Driving situation | 70% driving, 25% waiting, 5% stopped |
Power-supply voltage | Single phase 200-240V |
CO2 Coefficient | 0.519kg-CO2 / kWh |
DC power in
Power consumption and CO2 emissions reduced by 43% compared to previous models (compared to our previous models)
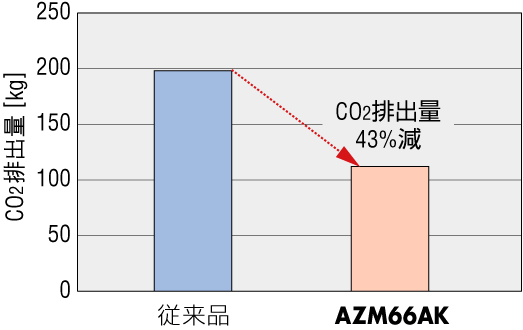
Operating conditions
Rotational speed | 1000r/min |
Load factor | 50% |
Operating time | 24-hour continuous operation, 365 days a year |
Driving situation | 70% driving, 25% waiting, 5% stopped |
Power-supply voltage | DC24V |
CO2 Coefficient | 0.519kg-CO2 / kWh |
Stable and fast without adjustments, a fusion of closed loop and open loop
Normally, it operates under open loop control, but when overloaded, it operates under closed loop control.
There are various advantages to using open loop control under normal conditions, and
by automatically switching to closed loop control in the event of an overload, it prevents abnormal stops.
Advantages of Open Loop Control
Moves in sync with commands without gain adjustment
Even mechanisms with low rigidity such as timing belts can follow commands without adjustment.
Even with changing load conditions, it operates seamlessly with the command.
Mechanisms with significant load variations, such as cams, can adhere to commands without requiring adjustments.
No hunting
It can be used safely even in applications where minute vibrations when the motor is stopped are a problem.
Advantages of Closed Loop Control
When the motor is overloaded, the torque is controlled to be maximized, preventing problems such as the motor stalling due to insufficient torque.
Extensive monitoring functions
The motor is equipped with a sensor, so position and speed information can be constantly monitored.
There is also a “positioning completion signal” that is useful for monitoring the operating status.
Types and features of geared motors
The motor is available in two connection methods
Cable type: Connect multiple cables | Connector type Direct connection with one cable Features and benefits of the connector type can be found here |
---|---|
![]() | ![]() |
- *The price is for an AC power input, mounting dimension 42 mm, electromagnetic brake, 3 m cable, and pulse train input driver.
Protection class IP66 specification (connector type)
With a protection rating of IP66, it is highly dustproof and can be used in environments where water droplets may splash on it.
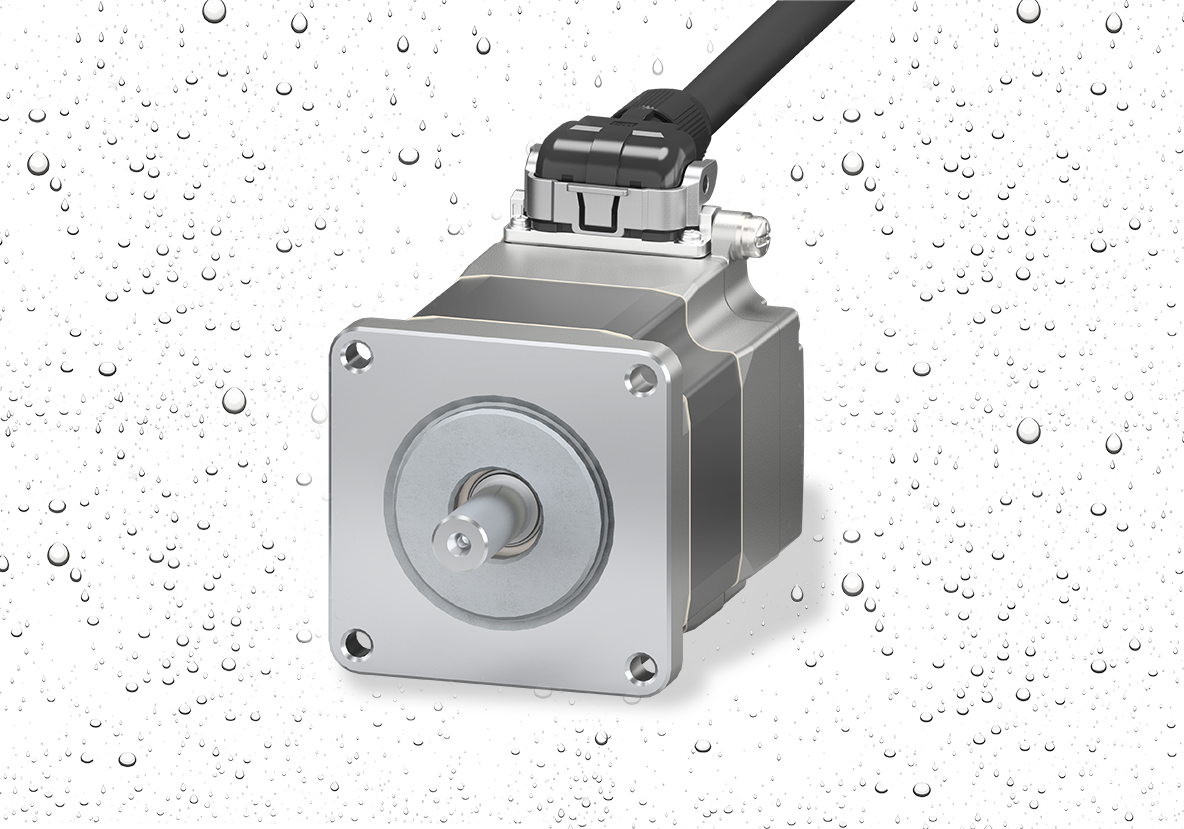
Connector Structure
The connector structure incorporates a gasket and O-ring for improved waterproofing. The connector as well is compliant with IP66.

Geared type types and features
In addition to providing high torque and high resolution, it offers various benefits such as the ability to drive large inertia loads.
type | Features | Mounting angle dimensions [mm] | Backlash [arcmin] | Resolution (when set to 1000P/R) [゜/pulse] | |
---|---|---|---|---|---|
TS Geared | ![]() |
| 42 to 90 | 10–45 | 0.012 to 0.1 |
Right-angle shaft FC geared | ![]() |
| 35, 42, 60 | 10–40 | 0.012 to 0.05 |
PS Geared | ![]() |
| 28–90 | 7–35 | 0.0072 to 0.072 |
HPG Geared | ![]() |
| 40–90 | 3 | 0.024 to 0.072 |
Harmonic Geared | ![]() |
| 30–90 | 0 | 0.0036 to 0.0072 |
Driver types and features
Network-enabled drivers
Compatible with major FA networks used around the world, it contributes to centralized management of device information and reduced wiring. AC power input drivers have better torque than DC power input, and DC power input drivers are smaller than AC power input drivers. Please consider which driver suits your purpose and application.
AC power in DC power in
![]() | ![]() | ![]() |
EtherCAT compatible | EtherNet/IP compatible | PROFINET compatible |
AC power input DC power input | AC power input DC power input | AC power input DC power input |
![]() | ![]() | ![]() |
MECHATROLINK-Ⅲ compatible | SSCNETⅢ/H compatible | Positioning function built-in type |
AC power in | AC power in | AC power input DC power input |
Mini driver (DC power input only)
This mini driver is designed to be even smaller and lighter than the single-axis driver. It can be installed in a small space. Its wide voltage specification allows it to be used with battery power, making it suitable for incorporation into self-propelled devices.
Multi-axis driver (DC power input only)
This is a multi-axis driver that can control multiple axes (up to 4 axes) with one driver. Connections to the host network and power supply are consolidated into one driver, contributing to reduced wiring, space savings, and cost reduction.
- EtherCAT® is a patented technology licensed from Beckhoff Automation GmbH (Germany) and is a registered trademark.
- EtherNet/IP™ is a trademark of ODVA.
- PROFINET is a trademark or registered trademark of PROFIBUS Nutzerorganisation eV (PNO).
- Modbus is a registered trademark of Schneider Automation Inc.
- Ethernet is a registered trademark of Fujifilm Business Innovation Co., Ltd.
- MECHATROLINK is a registered trademark of the MECHATROLINK Association.
- SSCNETⅢ/H is a registered trademark of Mitsubishi Electric Corporation.
Positioning function built-in type
- Operation data such as “position” and “speed” are set in the driver, and the operation data is selected and executed using an I/O unit, etc. Up to 256 pieces of operation data can be registered.
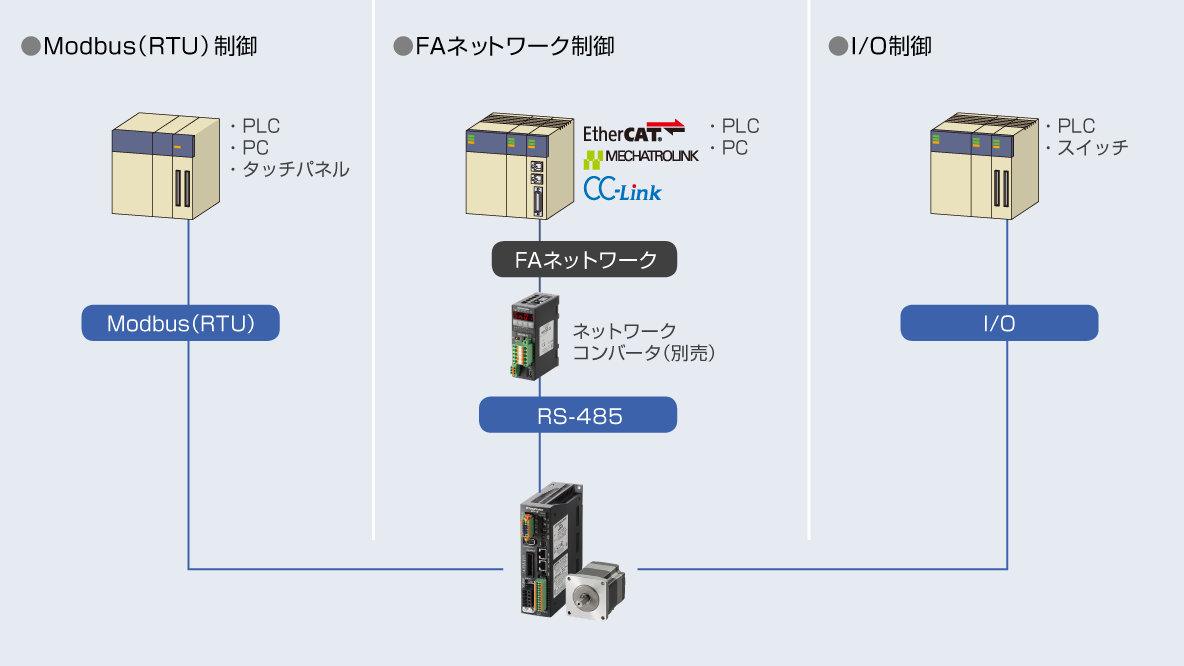
- CC-Link is a registered trademark of the CC-Link Partner Association.
- MECHATROLINK is a registered trademark of the MECHATROLINK Association.
- EtherCAT® is a patented technology licensed from Beckhoff Automation GmbH (Germany) and is a registered trademark.
- Modbus (RTU) is a registered trademark of Schneider Automation Inc.
Pulse train input type with RS-485 communication
The driver performs operation according to the pulse signal input. It is controlled by a positioning unit (pulse generator), etc. Motor status information (position, speed, alarm, etc.) can be monitored via RS-485 communication.
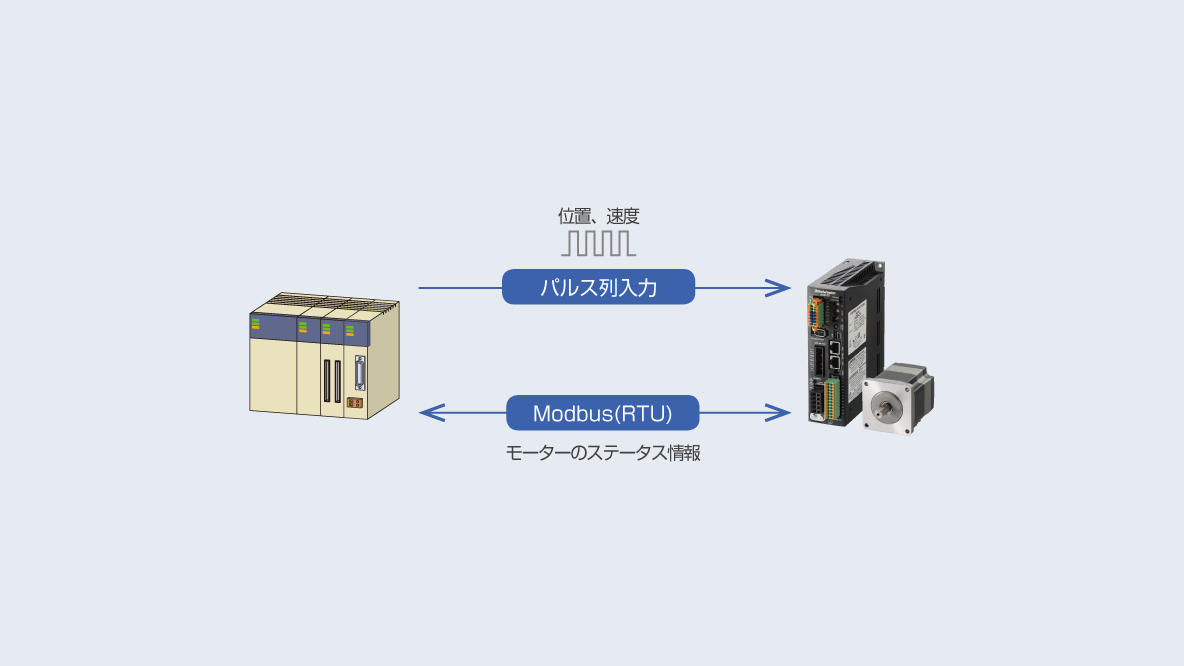
*Modbus (RTU) is a registered trademark of Schneider Automation Inc.
Pulse train input type
The driver performs operations according to the pulse signals input to it, and is controlled by a positioning unit (pulse generator) etc.
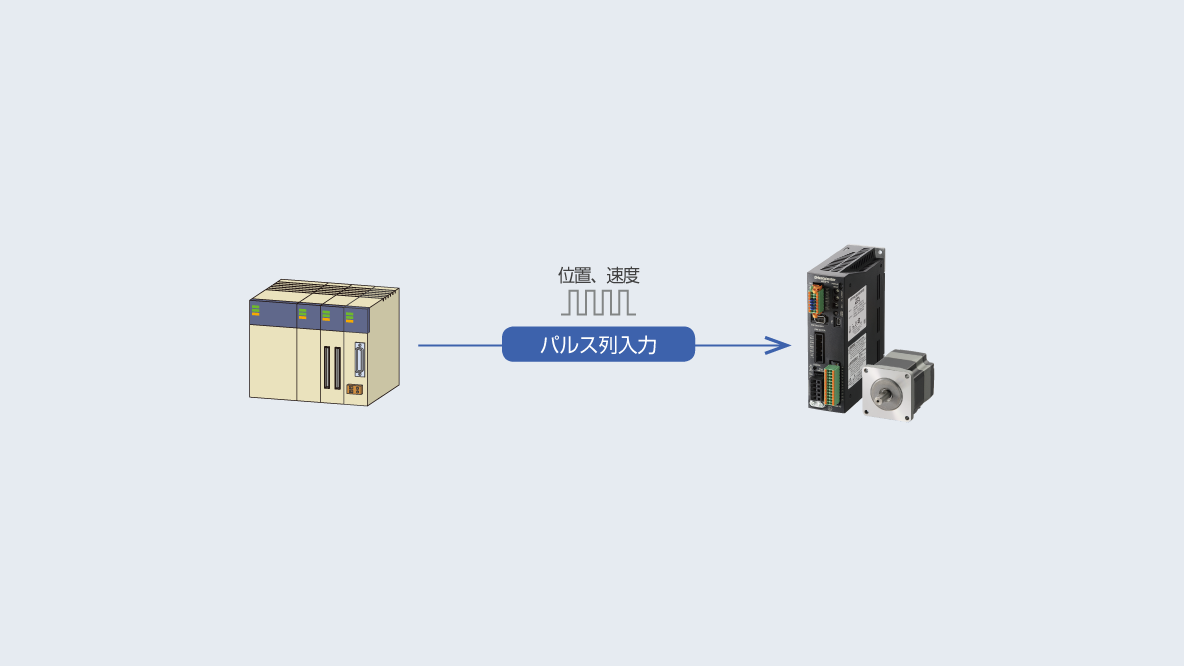
Acquisition of “Functional Safety” Certification
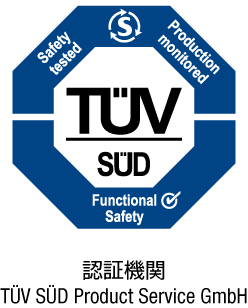
Having acquired “functional safety * ” certification, it has become easier to support safety systems. It reduces the number of peripheral devices, simplifies wiring, and saves space.
*Equipped with STO (Safe Torque Off) function
Certified for functional safety SIL 3, PL e
Compliance standards | Safety Integrity Level |
---|---|
IEC 61800-5-2, EN 61800-5-2 | SIL 3 |
IEC 61508-1, EN 61508-1 | |
IEC 61508-2, EN 61508-2 | |
ISO 13849-1, EN ISO 13849-1 | PL e (Category 3) |
Products
αSTEP AZ Series AC Power Input Driver
- EtherCAT compatible
- EtherNet/IP™ compatible
- PROFINET compatible
- MECHATROLINK-Ⅲ compatible
- SSCNETⅢ/H compatible
- Positioning function built-in type
- Pulse train input type with RS-485 communication
- Pulse train input type
Testing and monitoring with support software
Easily control from a PC using the support software MEXE02
A variety of functions provide comprehensive support from start-up to maintenance
We provide functions that are useful for wiring checks and test runs.
- Setting and saving operation data
- I/O Monitor
- Teaching/Remote Operation
We provide functions that are useful for adjusting motor operation after the equipment is installed.
- Waveform Monitor
- Alarm Monitor
- Unit Information Monitor
- Status Monitor
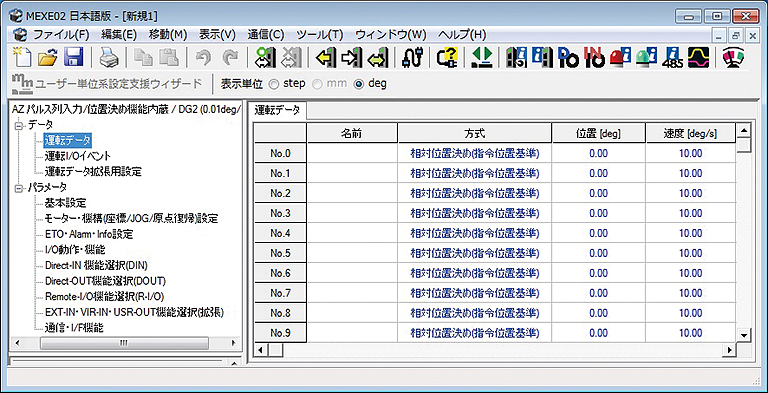
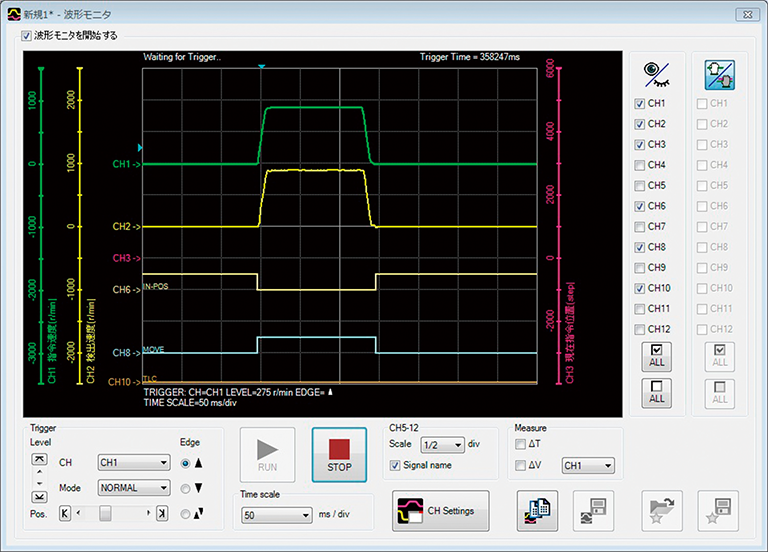
Related Products
-
TOYO KENSETSU KOHKI FM-2000 MESH BENDER
-
Hammer Caster 700K Twin-wheel Caster
-
U_RD CTL-12-S30-10Z AC current sensor
-
OSC 92TH300 Bio Box (Heat Insulation Box)
-
Chiyoda Seiki Pistol Small Type Welder For Welding And Heating Work From Thin To Thick Plates (For AC)
-
Eagle Jack (Konno Corporation) SDL-30FC Smart Dolly