Yamashina Seiki
Yamashina Seiki Tiltable Barrel Polishing Machine
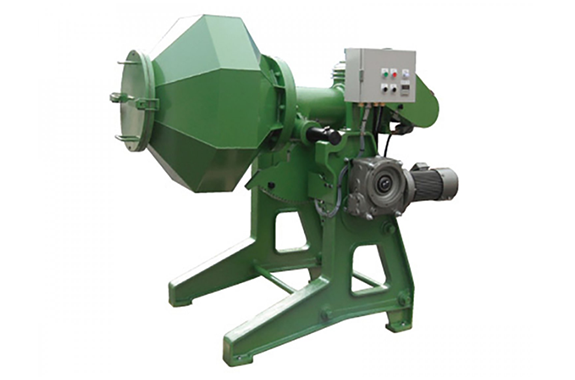
Product Made In Japan
Manufacture: Yamashina Seiki
What is Barrel Polishing?
Barrel polishing involves putting the work (product), media (polishing stone), compound (abrasive), water, etc. into a barrel tank (tank), applying constant rotational motion, stirring, and creating burrs by mutual friction. This is a finishing method that can be used to remove burrs, remove scale, and give a glossy finish. Once the working conditions are determined, a uniform finish with no variations can be obtained at any time, making it suitable for finishing mass-produced products.
Use/Purpose
Chamfering, burr removal, gloss finishing after machining
Chamfering, burr removal, gloss finishing of pressed
products Chamfering, gloss finishing of glass and ceramic products Matting
of plastic products
Removal of scale after heat treatment
After forging and die casting products Deburring,
base finishing before plating and painting,
degreasing, mixing, etc. in addition to polishing
Seven Features of Yamashina Tilting Barrel Polishing Machine
- Efficient tank shape with a long fluidized bed and increased polishing The
double octagonal pyramidal barrel tank has a unique shape to Yamashina barrels, and the triple action of the flowing filler and high pressure ensure that the contents are well mixed, resulting in efficient polishing. and polishing will be done. - Protects the workpiece
The rubber lining inside the barrel tank has sufficient thickness and appropriate hardness, providing excellent durability and protection of the workpiece. - Rational Elevation Device
Gears allow the barrel to be elevated quickly and safely. The elevation can be fixed at any angle, and the barrel tank can be rotated while tilted. - By changing the V-belt with variable speed function
or controlling it with an inverter, it is possible to supplement all the rotational speeds required for barrel polishing. - Reduced work time
The lid can be attached and removed easily and quickly because it is tightened with a toggle handle without the use of tools, making it easy to take in and take out contents and inspect. - Excellent safety and waterproofness
Stable operation is possible simply by placing the aircraft on a level floor. In addition, the mechanical parts are waterproof so that there is no problem even if they are exposed to water. - High durability and low power consumption
The structure is simple, robust, and carefully and precisely designed. It has great durability and rotation is extremely light and smooth, so it consumes less electricity.
Tank Direct Drive Type Barrel Polishing Machine
Features
- Possible to process workpieces with high specific gravity
- The structure is extremely simple and requires less maintenance.
- Rotation speed control by interval
- Tank tilting is possible with button operation
Specification
Model | 120HD | 200HD | 250HD | |
---|---|---|---|---|
Tank capacity (L) | 120 | 200 | 250 | |
Filling amount (L) | 72 | 120 | 150 | |
Motor (kW) | 2.2 | 3.7~5.5 | ||
Number of revolutions | 60Hz | ~36 | ||
min-1 | 50Hz | ~36 | ||
Aircraft weight (kg) | 300 | 900 | 950 | |
Standard paint color | 10GY6.5/6 | |||
lining | Rubber lining (7mm) |
Size
(mm)
format | A | B | C | D | E | F | G | H | X | Y |
---|---|---|---|---|---|---|---|---|---|---|
120HD | 1435 | 835 | 1490 | 850 | 280 | 670 | 710 | 680 | 230 | 525 |
200HD | 1720 | 1320 | 1795 | 1060 | 395 | 1120 | 850 | 800 | 230 | 625 |
250HD | 1800 | 1320 | 1870 | 1060 | 310 | 1120 | 850 | 850 | 350 | 640 |
Automatic Tilting Barrel Polishing Machine
Features
Tank tilting is possible with button operation
Specification
Model | 32H | 65H | 120H | 200H | 250H | |
---|---|---|---|---|---|---|
Tank capacity (L) | 32 | 65 | 120 | 200 | 250 | |
Filling amount (L) | 19 | 39 | 72 | 120 | 150 | |
Motor (kW) | 0.75 | 0.75 | 0.75 | 2.2 | 2.2 | |
Number of revolutions | 60Hz | 9,15,21,30,40 | 7,11,16,22,30 | 10,14,20,27 | ||
min-1 | 50Hz | 7,12,17,25,33 | 6,9,13,18,25 | 8,11,16,23 | ||
Aircraft weight (kg) | 180 | 200 | 300 | 900 | 950 | |
Standard paint color | 10GY6.5/6 | |||||
lining | Rubber lining (7mm) |
Size
format | A | B | C | D | E | F | G | H | X | Y |
---|---|---|---|---|---|---|---|---|---|---|
32H | 1070 | 780 | 1230 | 675 | 300 | 620 | 620 | 440 | 170 | 340 |
65H | 1160 | 780 | 1310 | 675 | 215 | 620 | 620 | 550 | 210 | 420 |
120H | 1311 | 835 | 1490 | 850 | 260 | 670 | 710 | 680 | 230 | 550 |
200H | 1585 | 1140 | 1795 | 1060 | 395 | 940 | 850 | 800 | 230 | 625 |
250H | 1660 | 1140 | 1910 | 1060 | 280 | 940 | 850 | 850 | 350 | 690 |
Manual Tilting Barrel Polishing Machine
Features
- Standard machine with tilting barrel
- Ideal for polishing small workpieces
Specification
Model | 32B | 65B | 120A | |
---|---|---|---|---|
Tank capacity (L) | 32 | 52 | 120 | |
Filling amount (L) | 19 | 39 | 72 | |
Motor (kW) | 0.75 | 0.75 | 0.75 | |
Number of revolutions | 60Hz | 9,15,21,30,40 | 7,11,16,22,30 | |
min-1 | 50Hz | 7,12,17,25,33 | 6,9,13,18,25 | |
Aircraft weight (kg) | 170 | 190 | 300 | |
Standard paint color | 10GY6.5/6 | |||
lining | Rubber lining (7mm) |
Size (mm)
format | A | B | C | D | E | F | G | H | X | Y |
---|---|---|---|---|---|---|---|---|---|---|
32B | 1070 | 763 | 1230 | 675 | 300 | 620 | 620 | 440 | 170 | 340 |
65B | 1160 | 763 | 1310 | 675 | 215 | 620 | 620 | 550 | 210 | 420 |
120A | 1311 | 814 | 1520 | 850 | 260 | 670 | 710 | 680 | 230 | 550 |
Option
We have options that can be used effectively when using barrel polishing machines. We can also accommodate specifications other than those listed in our lineup, so please feel free to contact us.
Operation of Tilting Barrel Polishing Machine
Tilting Barrel Polished Finish
After-sales service
We provide after-sales services such as supplying after-sales parts for various barrels, handling media and compounds, inspecting and maintaining the main body, and replacing the rubber lining of barrel tanks.
Media
We handle various sizes to suit different polishing applications.
shape | triangle | oblique cylinder | ball | rhombus | amorphous | cone |
---|---|---|---|---|---|---|
Purpose (variety) | K | N | R | H | – | – |
For extra heavy cutting (XX) | 30×30×16 25×25×14 20×20×12 15×15×10 12×12×12 10×10×7 8×8×8 6×6×6 5×5×5 4×4×4 3×3×3 | φ20×30 φ15×25 φ10×20 φ8×15 φ6×15 φ4.5×9 | φ0.3 φ0.5 φ0.7 φ2 φ3 φ4 φ5 φ6 φ7 φ8 φ10 φ12 φ15 φ20 φ25 | 50×35×20 60×45×25 | – | – |
For heavy cutting (X) | 30×30×16 25×25×14 20×20×12 15×15×10 12×12×12 10×10×7 8×8×8 6×6×6 5×5×5 4×4×4 3×3×3 | φ20×30 φ15×25 φ10×20 φ8×15 φ6×15 φ4.5×9 | φ0.3 φ0.5 φ0.7 φ2 φ3 φ4 φ5 φ6 φ7 φ8 φ10 φ12 φ15 φ20 φ25 | 50×35×20 60×45×25 | – | – |
For heavy cutting (YS) | – | – | – | – | 1~30mm | – |
For medium cutting (Y) | 30×30×16 25×25×14 20×20×12 15×15×10 12×12×12 10×10×7 8×8×8 6×6×6 5×5×5 4×4×4 3×3×3 | φ20×30 φ15×25 φ10×20 φ8×15 φ6×15 φ4.5×9 | φ0.3 φ0.5 φ0.7 φ2 φ3 φ4 φ5 φ6 φ7 φ8 φ10 φ12 φ15 φ20 φ25 | 50×35×20 60×45×25 | – | – |
For medium cutting (YSW) | – | – | – | – | 1~30mm | – |
For semi-finishing (G) | 30×30×16 25×25×14 20×20×12 15×15×10 12×12×12 10×10×7 8×8×8 6×6×6 5×5×5 4×4×4 3×3×3 | φ20×30 φ15×25 φ10×20 φ8×15 φ6×15 φ4.5×9 | φ0.3 φ0.5 φ0.7 φ2 φ3 φ4 φ5 φ6 φ7 φ8 φ10 φ12 φ15 φ20 φ25 | – | – | – |
For finishing (2Z) | – | – | φ0.3 φ0.5 φ0.7 φ2 φ3 φ4 φ5 φ6 φ7 φ8 φ10 φ12 φ15 φ20 φ25 | – | – | – |
For mirror finishing (TEP) | – | – | – | – | 1~9mm | – |
Plastic (PL) | – | – | – | – | – | φ10~50 |
*For YS, YSW, TEP, and PL, please check the size each time.
*We also handle steel balls, carborundum (SIC), alundum (A), styrene powder, dry media, etc.
*We also manufacture products in sizes other than those listed in the catalog, so please contact us.
Compound
Powder compound ◎ Recommended product ○ Applicable product × Non-conforming product
Product name | Processing purpose | Workpiece material | Features | |||||||||
---|---|---|---|---|---|---|---|---|---|---|---|---|
descaling | Degreasing | Rough finish | Semi-finishing | glossy finish | Rust prevention | iron/steel | stainless | aluminum | zinc | copper | ||
YL-310 | ◎ | ○ | ○ | ◎ | ○ | Ideal for descaling | ||||||
YL-320 | ○ | ◎ | ◎ | ○ | Very high rust prevention/low foaming | |||||||
YL-330 | ○ | ◎ | ◎ | Ideal for degreasing and rough finishing stainless steel /White shines in acidity | ||||||||
YL-340 | ◎ | ◎ | ○ | ◎ | × | × | × | × | Ideal for steel and rough finishing | |||
YL-350 | ○ | ◎ | ◎ | ◎ | High degreasing power, ideal for rough finishing | |||||||
YL-360 | ○ | ◎ | ◎ | ◎ | Very high degreasing power | |||||||
YL-370 | ◎ | ◎ | ◎ | ◎ | ◎ | Ideal for glossy finishes |
Liquid Compound
Product name | Processing purpose | Workpiece material | Features | |||||||||
---|---|---|---|---|---|---|---|---|---|---|---|---|
descaling | Degreasing | Rough finish | Semi-finishing | glossy finish | Rust prevention | iron/steel | stainless | aluminum | zinc | copper | ||
YL-6100 | ○ | ◎ | ◎ | ◎ | ○ | ◎ | Ideal for bright finishing of steel, stainless steel and copper | |||||
YL-6200 | ◎ | ○ | ◎ | ○ | Ideal for glossy finishing of steel/Low price and excellent cost performance | |||||||
YL-6300 | ○ | ◎ | ○ | ◎ | Ideal for glossy finishing of stainless steel/Low price and excellent cost performance | |||||||
YL-6400 | ◎ | ○ | ◎ | ○ | ○ | Ideal for glossy stainless steel finishes/ also effective for soft metals | ||||||
YL-6500 | ○ | ◎ | ◎ | ○ | High degreasing power and cleaning effect | |||||||
YL-6600 | ◎ | ◎ | ◎ | ○ | ○ | ○ | Good foam removal/almighty for glossy finishes |
Anti-rust
Product name | Processing purpose | Workpiece material | Features | |||||||||
---|---|---|---|---|---|---|---|---|---|---|---|---|
descaling | Degreasing | Rough finish | Semi-finishing | glossy finish | Rust prevention | iron/steel | stainless | aluminum | zinc | copper | ||
YL-A | ◎ | ◎ | ◎ | ○ | ○ | ○ | Water-soluble temporary rust preventive agent/Low price and excellent cost performance | |||||
YL-B | ◎ | ◎ | ◎ | ○ | ○ | ○ | Water-soluble temporary rust preventive agent/low foaming | |||||
YL-C | ◎ | ◎ | ◎ | Water displacement, medium- to long-term rust preventive agent |
*In addition to the compounds listed above, we can also manufacture the most suitable compound for your company according to your needs.
*It has been used stably for many years overseas as well.
*PRTR non-compliant products, low BOD, COD products, and products containing polishing accelerators are also available.
Regarding Consultation Regarding Barrel Polishing Technology
We conduct machining tests for parts that require barrel finishing at our research department at our head office.
If you send us your test work, we will respond with experimental data.
We also help select the most suitable media and compound, so please feel free to contact us.
Barrel Polishing Guide
situation | Cause |
---|---|
Unable to polish uniformly | 1. Bad shape or rotation of the barrel tank 2. Bad barrel installation |
It takes time to finish | 1. Rotation is too slow 2. Media is too small 3. Media is clogged 4. Filling amount is too high or too low 5. Too much water 6. Inappropriate selection of compound |
Causes scratches and dents and becomes deformed | 1. Insufficient filling amount 2. Improper mixing ratio of workpiece and media 3. Too fast rotation 4. Too little water amount 5. Workpiece surface is too rough |
No gloss on the finished surface | 1. Inappropriate compound 2. Severe dirt on the media or workpiece 3. Too fast rotation 4. Too little water volume 5. The surface of the workpiece is too rough |
Finishing Conditions For Barrel Processing
- Model, shape, and size of barrel polishing machine
- Type, shape, size, and amount of media
- Water use and its quality and quantity
- Compound type/amount
- Volume ratio of media and workpiece
- Filling amount in the barrel
- Rotational speed
- Machining time
- temperature
- Work material, shape, and size
Movement Diagram Inside The Barrel
Related Products
-
Yamashina Seiki TLDCN Type Timing Lubrication Cylinder Lubricator
-
Yamashina Seiki Vertical Guide Rail Automatic Processing Line For Elevator
-
Yamashina Seiki Tabletop R Chamfering Machine
-
Yamashina Seiki Food Cutter
-
Yamashina Seiki Transfer Machine for High-Pressure Gas Container Processing
-
Yamashina Seiki GP Type General Purpose Grease Pump