Atsuchi Tekko Co., Ltd., Japan
Ascon ACR New Wet Blaster
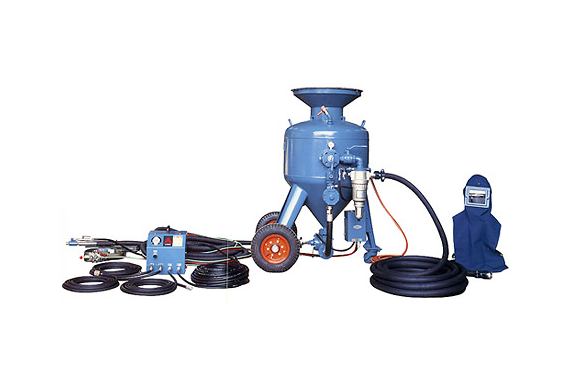
Made in Japan
Manufacturer: Ascon
Model: ACR New Wet Blaster
Features
The ACR New Wet Blaster attaches a wet nozzle holder to the nozzle and sprays water in a fog screen shape in accordance with the blast injection. It envelops dust from the outside to prevent scattering.
The wet nozzle uses the intake jet system to spray water on a fog screen, and can completely capture abrasives, debris, and fine dust. Therefore, it is now possible to easily perform blasting work in a clean environment with the same processing capacity.
Depending on the application, it can also be used as a dry blasting machine.
- Can be connected to your current blasting machine.
- The dust collection effect can be completely prevented down to fine dust.
- Since a temporary rust inhibitor mixture is used, it has excellent compatibility with painting.
- Dry blasting and processing capacity are almost the same.
- It is easy to check the cleaning surface and has excellent work efficiency.
- If baking soda, which is relatively harmless to the human body, is used as an abrasive, it becomes a baking soda blaster.
Handling
- Open the air source valve (set to pressure reducing valve 2 kg/cm3)
- Open the stirring valve.
- Fill the sump tank with water and drip an appropriate amount of rust inhibitor.
- Open the pressure control valve and pump the mixture with the air pressure reducing valve 2 kg/cm3 on flat ground.
When working in high places, there is no problem with work if the pressure is increased by 10 kg/cm1 for every 3 meters of rise. - Connect the mixture hose to the mixture release valve and open the discharge valve.
The wet blaster is now ready. - Connect the mixture hose to the holder at the end of the blast hose and attach the wet nozzle.
- Insert the nozzle into the tip injection port.
- Open the mixture flow control valve at the nozzle and perform the abrasive work.
If the amount of mixture is small, the wet blaster will not be fully effective. In consideration of dust scattering and the size of the abrasive particles, open the control valve. - After blasting, stop the injection of the abrasive, rinse the surface with only rust prevention liquid, and clean the surface without leaving a water film by air injection for moisture remaining on the surface.
Related Products
-
Yamamoto Keiki Class 0.6 Pressure Gauge
-
Vessel No.GT-NWS20 Double Action Air Nipper (Square Type)
-
SAKUSAKU SDHR61925C3 Internal Coolant Holder For Internal Grooving
-
Mikasa MCD-T18H Concrete Cutter
-
Tosei Sharyo GSH Series Manual Rotary Gold Lifter
-
Japan Clamp C-500 Clamp For Horizontal Suspension (With One-Touch Lock Device)