Japan
Automatic Ultrasonic Flaw Detector For Drive Pinion Forgings
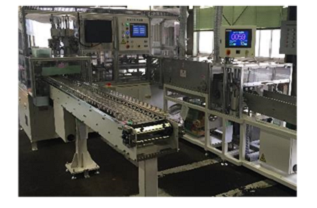
Made in Japan
Feature:
This ultrasonic flaw detector is used to measure the dimensions and runout of drive pinions manufactured by cold forging and to detect chevron cracks that occur inside the pinions.
The operator sets several dozen workpieces in the stocker to start the inspection, and the workpieces are transferred to the outgoing stocker after length measurement, thickness measurement, runout measurement, flaw detection, draining, drying, and rejection of defects.
Specifications:
(1) Target workpiece
- Shape: Φ72mm or less, length≦300mm
- Material: Steel, cold-forged
- Inspection area : Shaft area
(2) Flaw Detection Method and Inspection Performance
- Flaw Detection Method :Ultrasonic immersion method K-scanning and pulse reflection
- Target flaw: Chevron crack
- Measurement accuracy: ±0.1mm
- Detection performance: 0.5mm FBH
- Processing capacity: 10 sec/pc. or less
Related Products
-
Watanabe WTM-PE6L Web-enabled Energy Monitoring Module
-
Howa MBN-350VCT1K Vertical Machining Center (Inline Type/MBN-Series)
-
Watanabe WRBC-DIO8DF/WRBC-DIO8SF Digital Input/output module – Remote I/O
-
SAKUSAKU GYG74040 Square End Mill 4-Flute
-
Shizuoka Seiki RKF 506-A Evaporative Air Cooler
-
IMADA EB/EN/RE series Hoisting Attachment for High Capacity Load Cell