Japan, Steel Material, Sumitomo Denko
Sumitomo Anti Corrosion Steel Material Epoxy Strand
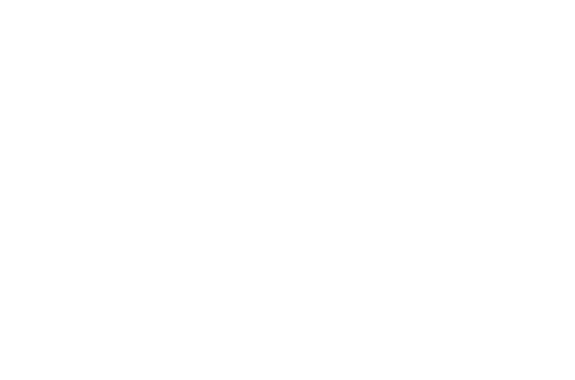
Product: Made In Japan
Manufacturer: Sumitomo
Model: Steel Material
Appearance
Epoxy Strand is an anti-corrosion steel material that is coated with high-quality epoxy powder on PC steel wires. It was developed to enhance the durability of cables. It is highly regarded for its corrosion resistance, especially in applications such as salt-damaged bridges, non-grout external cables, and ground anchors, where high corrosion resistance is required in our country’s anti-corrosion steel materials.
Furthermore, the epoxy coating provides improved fatigue resistance compared to regular PC steel wires, making it suitable for use in “extradosed” bridges.
*Epoxy strand *Polyethylene coated Froguard * Flobond
Structure
Examples of installation locations
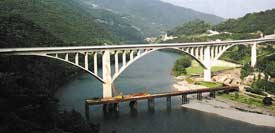
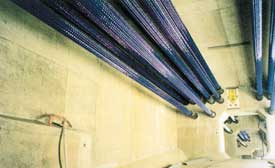
The ratio of the number of application experiments of epoxy strands in the field of bridges
“Benefits of Using Epoxy Strands in External Cables Applying epoxy strands to non-grout external cables offers several advantages compared to grout-filled external cables:
- Labour savings and shortened construction period due to omission of grout work.
- Omission of the connection and installation work of long polyethene protective tubes.
- Reduction in the cable’s self-weight.
- Easy cable inspection even after being put into service.
- Corrosion protection throughout the entire period from manufacturing to storage, installation, and operation.”
Dimensions and Mechanical Properties
Symbol | Name | Basic Dimensions (mm) | Film Thickness (μm) | Unit Weight (kg/km) | Load for 0.2% Permanent Elongation (kN) | Tensile Load (kN) | Elongation (%) | Relaxation (%) after 1000 hours |
---|---|---|---|---|---|---|---|---|
ESWP7A | 12.4 | 13.6 | 400-1200 | 765 | 136 or more | 160 or more | 3.5% or more | Less than 6.5% |
15.2 | 16.4 | 1,155 | 204 or more | 240 or more | 3.5 or more | |||
ESWP7B | 12.7 | 13.9 | 813 | 156 or more | 183 or more | 3.5 or more | ||
15.2 | 16.4 | 1,155 | 222 or more | 261 or more | 3.5 or more |
- ※1: “Crown section”
- ※2: “In accordance with JIS G 3536-1999”
Key Technical Data
Item | Description |
---|---|
Salt Spray Test | Conforms to ASTM B117-73. No abnormalities observed in the coating after 3000 hours<br>(Under stress at 70% of the tensile strength) |
Underground Exposure Test | Under tension load (0.6Pu), no coating deterioration, and no rust compared to PC steel wire after 7 years |
Composite Cycle Test | No abnormalities observed over 6 months |
Adhesion Performance | Comparable to bare PC steel wire |
Standard Set Loss | 9mm |
Friction Coefficient (Within Polyethylene Sheath) | M=0.3(1/rad) or less <br> λ=0.004(1/m) or less |
Regulations (Reference) Regarding Epoxy Strand Coating Thickness
Standard | Range of Coating Thickness | Measurement Method |
---|---|---|
ASTM (A882-2002) | 0.38 – 1.14 mm | Electromagnetic thickness gauge. Measure one point for every 600m of the product. Measure the thickness of the crown area (Figures 1 to 6) at each measurement point. |
ISO (14655-1999) | Non-fill Type: 0.65 – 1.15 mm<br> Fill Type: 0.40 – 0.90 mm | Electromagnetic thickness gauge. Divide one product into approximately five equal parts and use these five positions as measurement points. Measure the thickness of the crown area (Figures 1 to 6) at each measurement point and calculate the average of the six data points as the measurement value. |
JIS (Draft) | Crown Area (Fill Type Only) – Average of 6 positions: 0.5 – 0.9 mm<br> Each Crown Area: 0.4 – 1.2 mm | Optical microscope. Measure one point at the end of one product as the measurement point. Measure the thickness of the crown area (Figures 1 to 6) at the measurement point. |
Adherence of the Coating Film Until the Breakage of the Steel Material
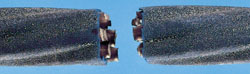
Can be directly anchored over the coating film using specialized anchoring devices
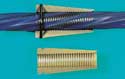
Comparison with conventional material after 1000 hours of salt spray
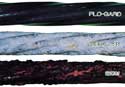
Important Notices
- Use specialized equipment and components for tension and anchoring.
- When unloading and moving, use a forklift, hoist, or similar equipment to prevent damage to the epoxy surface.
- When inserting, take care to prevent the wire from rubbing against metal objects such as conduit pipes.
- In case of any damage, repair it using epoxy paint specified by the manufacturer.
- Ensure that the bending radius does not exceed the drum diameter.
- Do not perform electric welding or gas cutting.
- Avoid contact with sparks generated during electric welding or gas cutting of reinforcement bars, iron plates, etc.
- Store indoors or cover to protect from prolonged direct sunlight.
- Remove any dirt or foreign substances, as they may affect adhesion performance and bonding with concrete.
- Do not use epoxy coating alone in environments exposed to direct UV radiation.
- When used as pre-tensioning material, release tension at a concrete temperature below 65°C.
- Refer to the handling manual for instructions when using this product.
Related Products
-
Okazaki Seiko SED2A Coated Solid Carbide Square Endmills (2 Flutes)
-
TSUBOSAN Square 150mm Engineer’s Files
-
Nippon Chemical Screw KJPA/NT(M) KYOUJIN/Hex Nut
-
Fujii Denko 57C Pole Safety Belt
-
REX Shut-Off Tool 50, 75, 100 Plastic pipe tools
-
Kondotec Backing Material For Non-scarp Welding Method (SN490B)